Entre todos los tipos existentes de destrucción de metales, el más común es la corrosión electroquímica, que se produce como resultado de su interacción con un medio electrolíticamente conductor. La principal razón de este fenómeno es la inestabilidad termodinámica de los metales en los ambientes que los rodean.
Muchos objetos y estructuras son susceptibles a este tipo de corrosión:
- tuberías de gas y agua;
- elementos de vehículos;
- otras estructuras hechas de metal.
Los procesos corrosivos, es decir, la oxidación, pueden ocurrir en la atmósfera, en el suelo e incluso en el agua salada. Limpiar estructuras metálicas de manifestaciones de corrosión electroquímica es un proceso complejo y largo, por lo que es más fácil prevenir su aparición.
Variedades principales
Durante la corrosión de los electrolitos, la energía química se convierte en energía eléctrica. En este sentido, se llama electroquímico. Se acostumbra distinguir los siguientes tipos de corrosión electroquímica.
intercristalino
La corrosión intergranular se refiere a un fenómeno peligroso en el que los límites de grano del níquel, el aluminio y otros metales se destruyen de forma selectiva. Como resultado, se pierden la resistencia y las propiedades plásticas del material. El principal peligro de este tipo de corrosión es que no siempre se nota visualmente.
picaduras
La corrosión electroquímica por picaduras es una lesión puntual de áreas individuales de la superficie del cobre y otros metales. Dependiendo de la naturaleza de la lesión, se distinguen fóveas cerradas, abiertas y superficiales. El tamaño de las zonas afectadas puede variar de 0,1 mm a 1,5 mm.
Ranurado
La corrosión electroquímica de grietas comúnmente se denomina proceso intensificado de destrucción de estructuras metálicas en lugares de grietas, huecos y grietas. La corrosión por grietas puede ocurrir en el aire, mezclas de gases y agua de mar. Este tipo de destrucción es típica de los gasoductos, los fondos de los buques y muchos otros objetos.
La corrosión ocurre en condiciones de una pequeña cantidad de oxidante debido al difícil acceso a las paredes de la grieta. Esto provoca la acumulación de productos corrosivos en el interior de los huecos. El electrolito contenido en el espacio interno del espacio puede cambiar bajo la influencia de la hidrólisis de los productos de corrosión.
Para proteger los metales de la corrosión por grietas, es común utilizar varios métodos:
- sellar huecos y grietas;
- protección electroquímica;
- proceso de inhibición.
Como métodos preventivos, se deben utilizar solo aquellos materiales que sean menos susceptibles a la oxidación y también diseñar inicialmente de manera correcta y racional las tuberías de gas y otros objetos importantes.
Una prevención competente es en muchos casos un proceso más sencillo que la limpieza posterior de estructuras metálicas del óxido arraigado.
Cómo se manifiestan los diferentes tipos de corrosión
Un ejemplo del proceso de corrosión es la destrucción de diversos dispositivos, componentes de automóviles, así como cualquier estructura de metal y ubicada:
- en el aire atmosférico;
- en aguas: mares, ríos contenidos en el suelo y debajo de capas de suelo;
- en entornos técnicos, etc.
Durante el proceso de oxidación, el metal se convierte en una celda galvánica multielectrónica. Así, por ejemplo, si el cobre y el hierro entran en contacto en un medio electrolítico, el cobre es el cátodo y el hierro es el ánodo. Al donar electrones al cobre, el hierro en forma de iones ingresa a la solución. Los iones de hidrógeno comienzan a moverse hacia el cobre y se descargan allí. Al volverse cada vez más negativo, el cátodo pronto se vuelve igual al potencial del ánodo, como resultado de lo cual el proceso de corrosión comienza a disminuir.
Los diferentes tipos de corrosión se manifiestan de diferentes maneras. La corrosión electroquímica se manifiesta más intensamente en los casos en que el cátodo contiene inclusiones de metal con menor actividad en comparación con el que se corroe: el óxido aparece más rápido y es bastante expresivo.
La corrosión atmosférica ocurre en aire húmedo y temperaturas normales. En este caso, se forma una película de humedad con oxígeno disuelto en la superficie del metal. El proceso de destrucción del metal se intensifica a medida que aumenta la humedad del aire y el contenido de óxidos gaseosos de carbono y azufre, siempre que:
- grietas;
- aspereza;
- otros factores que facilitan el proceso de condensación.
La corrosión del suelo afecta sobre todo a una variedad de estructuras subterráneas, gasoductos, cables y otras estructuras. La destrucción del cobre y otros metales se produce debido a su estrecho contacto con la humedad del suelo, que también contiene oxígeno disuelto. La destrucción de las tuberías puede ocurrir ya seis meses después de su construcción si el suelo en el que están instaladas se caracteriza por una alta acidez.
Bajo la influencia de corrientes parásitas que emanan de objetos extraños, se produce corrosión eléctrica. Sus principales fuentes son los ferrocarriles eléctricos, las líneas eléctricas, así como las instalaciones especiales que funcionan con corriente eléctrica continua. En mayor medida, este tipo de corrosión provoca destrucción:
- gasoductos;
- todo tipo de estructuras (puentes, hangares);
- cables eléctricos;
- oleoductos.
La acción de la corriente provoca la aparición de zonas de entrada y salida de electrones, es decir, cátodos y ánodos. El proceso destructivo más intenso se produce en las zonas con ánodos, por lo que allí el óxido se nota más.
La corrosión de componentes individuales de las tuberías de gas y agua puede deberse al hecho de que el proceso de instalación es mixto, es decir, se produce utilizando diferentes materiales. Los ejemplos más comunes son la corrosión por picaduras que se produce en elementos de cobre, así como la corrosión de bimetales.
Con una instalación mixta de elementos de hierro con aleaciones de cobre y zinc, el proceso de corrosión es menos crítico que con la fundición de cobre, es decir, con aleaciones de cobre, zinc y estaño. La corrosión de las tuberías se puede prevenir mediante métodos especiales.
Métodos de protección contra el óxido.
Se utilizan varios métodos para combatir la oxidación insidiosa. Veamos aquellos que son los más efectivos.
Método número 1
Uno de los métodos más populares es la protección electroquímica de hierro fundido, acero, titanio, cobre y otros metales. ¿En qué se basa?
El procesamiento electroquímico de metales es un método especial destinado a cambiar la forma, el tamaño y la rugosidad de la superficie mediante disolución anódica en un electrolito bajo la influencia de una corriente eléctrica.
Para garantizar una protección confiable contra la oxidación, es necesario tratar los productos metálicos con medios especiales, que contienen diversos componentes de origen orgánico e inorgánico, incluso antes de su uso. Este método te permite evitar la aparición de óxido durante un tiempo determinado, pero luego tendrás que renovar el revestimiento.
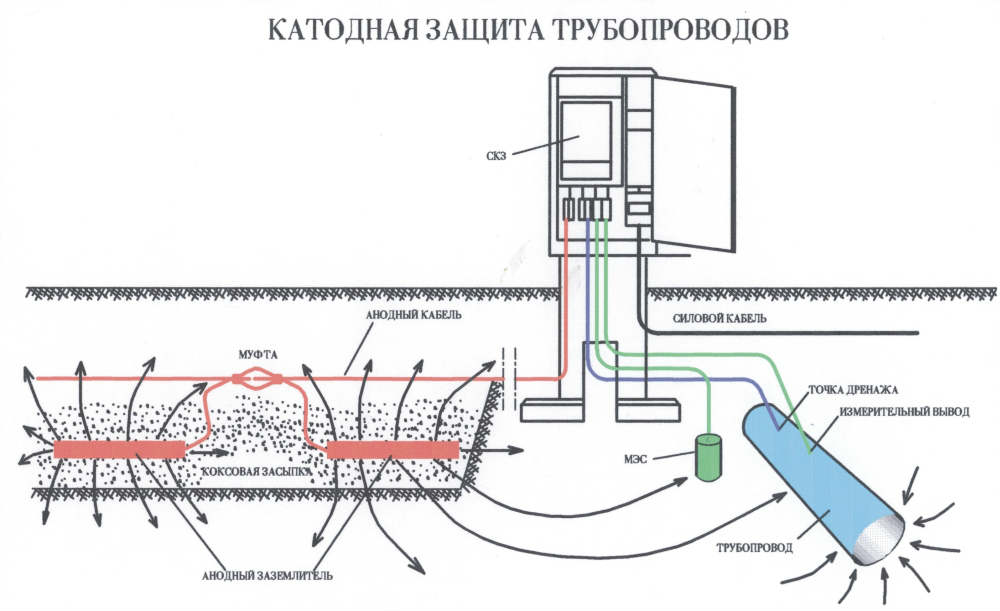
La protección eléctrica es un proceso en el que se conecta una estructura metálica a una fuente externa de corriente eléctrica directa. Como resultado de esto, se forma la polarización de los electrodos de tipo catódico en su superficie y todas las regiones anódicas comienzan a transformarse en catódicas.
El procesamiento electroquímico de metales puede ocurrir con la participación de un ánodo o cátodo. En algunos casos, se produce un procesamiento alternativo de un producto metálico con ambos electrodos.
La protección catódica contra la corrosión es necesaria en situaciones en las que el metal a proteger no tiene predisposición a la pasivación. Se conecta una fuente de corriente externa al producto metálico: una estación de protección catódica especial. Este método es adecuado para proteger tuberías de gas, así como tuberías de suministro de agua y calefacción. Sin embargo, este método tiene ciertas desventajas en forma de agrietamiento y destrucción de las capas protectoras; esto ocurre en casos de un cambio significativo en el potencial del objeto en la dirección negativa.
Método número 2
El procesamiento de metales por electrochispa se puede llevar a cabo utilizando varios tipos de instalaciones: sin contacto, con contacto y también anódico-mecánicas.
Método número 3
Para proteger de forma fiable los gasoductos y otras tuberías contra la oxidación, a menudo se utiliza un método como la pulverización por arco eléctrico. Las ventajas de este método son obvias:
- espesor significativo de la capa protectora;
- alto nivel de rendimiento y confiabilidad;
- uso de equipos relativamente económicos;
- proceso tecnológico simple;
- posibilidad de utilizar líneas automatizadas;
- bajos costos de energía.
Entre las desventajas de este método se encuentran la baja eficiencia al procesar estructuras en ambientes corrosivos, así como una fuerza de adhesión insuficiente a la base de acero en algunos casos. En cualquier otra situación, dicha protección eléctrica es muy eficaz.
Método número 4
Para proteger una variedad de estructuras metálicas (gasoductos, estructuras de puentes, todo tipo de tuberías), se requiere un tratamiento anticorrosión eficaz.
Este procedimiento se lleva a cabo en varias etapas:
- eliminación completa de depósitos grasos y aceites utilizando disolventes eficaces;
- la limpieza de la superficie tratada de sales solubles en agua se realiza mediante aparatos profesionales de alta presión;
- eliminación de errores estructurales existentes, alineación de bordes: esto es necesario para evitar que la capa de pintura aplicada se descascarille;
- limpieza a fondo de la superficie con un chorro de arena; esto se hace no solo para eliminar el óxido, sino también para dar el grado deseado de rugosidad;
- aplicación de material anticorrosión y una capa protectora adicional.
Un correcto pretratamiento de gasoductos y todo tipo de estructuras metálicas les proporcionará una protección fiable contra la corrosión electroquímica durante el funcionamiento.