Одним из наиболее распространенных и в то же время губительных факторов, воздействующих на автомобиль в процессе эксплуатации, выступает коррозия. Разработано несколько способов защиты кузова от нее, причем встречаются как меры, направленные именно против данного явления, так и комплексные технологии защиты автомобиля, предохраняющие его от различных факторов. В приведенной статье рассмотрена электрохимическая защита кузова.
Причины образования коррозии
Так как электрохимический способ защиты автомобиля направлен исключительно против коррозии, следует рассмотреть причины, вызывающие поражение ею кузова. Основными из них являются вода и дорожные реагенты, применяемые в холодный период. В сочетании друг с другом они образуют высококонцентрированный соленый раствор. К тому же осевшая на кузове грязь продолжительное время удерживает влагу в порах, а если она содержит дорожные реагенты, то еще и притягивает молекулы воды и из воздуха.
Ситуация усугубляется, если лакокрасочное покрытие автомобиля имеет дефекты, даже небольшого размера. В таком случае распространение коррозии будет происходить очень быстро, и даже сохранившиеся защитные покрытия в виде грунта и оцинковки могут не остановить этот процесс. Поэтому важно не только постоянно очищать автомобиль от грязи, но и следить за состоянием его лакокрасочного покрытия. В распространении коррозии также играют роль температурные колебания, а также вибрации.
Также следует отметить участки автомобиля, наиболее подверженные поражению коррозией. К ним относятся:
- детали, расположенные ближе всего к дорожному покрытию, то есть пороги, крылья и днище;
- сварные швы, оставшиеся после ремонта, особенно если он был неграмотно осуществлен. Это объясняется высокотемпературным «ослаблением» металла;
- кроме того, ржавчина часто поражает различные скрытые плохо вентилируемые полости, где скапливается влага и долго не высыхает.
Принцип действия электрохимической защиты
Рассматриваемый способ защиты кузова от ржавчины относят к активным методам. Разница между ними и пассивными способами состоит в том, что первые создают какие-либо защитные меры, не позволяющие вызывающим коррозию факторам воздействовать на автомобиль, в то время как вторые лишь изолируют кузов от воздействия атмосферного воздуха. Данная технология изначально применялась для защиты от ржавчины трубопроводов и металлоконструкций. Электрохимический метод считают одним из наиболее эффективных.
Данный способ защиты кузова, который также называют катодным, основан на особенностях протекания окислительно-восстановительных реакций. Суть состоит в том, что на защищаемую поверхность накладывают отрицательный заряд.
Сдвиг потенциала осуществляют с применением внешнего источника постоянного тока или путем соединения с протекторным анодом, состоящим из более электроотрицательного металла, чем защищаемый объект.
Принцип действия электрохимической защиты автомобиля состоит в том, что между поверхностью кузова и поверхностью окружающих объектов вследствие разности потенциалов между ними по цепи, представленной влажным воздухом, проходит слабый ток. В таких условиях окислению подвергается более активный металл, а другой, наоборот, восстанавливается. Именно поэтому используемые для автомобилей защитные пластины из электроотрицательных металлов называют жертвенными анодами. Однако при чрезмерном сдвиге потенциала в отрицательную сторону возможно выделение водорода, изменение состава приэлектродного слоя и прочие явления, которые приводят к деградации защитного покрытия и возникновению стресс-коррозии защищаемого объекта.
Рассматриваемая технология для автомобилей предполагает использование в качестве катода (отрицательно заряженного полюса) кузова, а анодами (положительно заряженными полюсами) служат различные окружающие объекты или установленные на автомобиле элементы, проводящие ток, например, металлические сооружения или влажное дорожное покрытие. При этом анод должен состоять из активного металла, такого как магний, цинк, хром, алюминий.
Во многих источниках приведена разность потенциалов между катодом и анодом. В соответствии с ними, чтобы создать полную защиту от коррозии для железа и его сплавов, необходимо достичь потенциал в 0,1-0,2 В. Большие значения слабо сказываются на степени защиты. При этом плотность защитного тока должна составлять от 10 до 30 мА/м².
Однако эти данные не совсем верны – в соответствии с законами электрохимии, расстояние между катодом и анодом прямо пропорционально определяет величину разницы потенциалов. Поэтому в каждом конкретном случае необходимо достичь определенного значения разницы потенциалов. К тому же воздух, рассматриваемый при данном процессе в качестве электролита, способен проводить электрический ток, характеризующийся большой разницей потенциалов (примерно кВт), поэтому ток с плотностью 10-30 мА/м² не будет проводиться воздухом. Возможно возникновение лишь «побочного» тока в результате намокания анода.
Что касается разности потенциалов, наблюдается концентрационная поляризация по кислороду. При этом попавшие на поверхность электродов молекулы воды ориентируются на них таким образом, что происходит освобождение электронов, то есть реакция окисления. На катоде данная реакция, наоборот, прекращается. Вследствие отсутствия электрического тока освобождение электронов происходит медленно, поэтому процесс безопасен и незаметен. Благодаря эффекту поляризации, происходит дополнительное смещение потенциала кузова в отрицательную сторону, что дает возможность периодически выключать устройство защиты от коррозии. Нужно отметить, что площадь анода прямо пропорционально определяет эффективность электрохимической защиты.
Варианты создания
В любом случае роль катода будет выполнять кузов автомобиля. Пользователю необходимо выбрать предмет, который будет использован в качестве анода. Выбор осуществляют на основе условий эксплуатации автомобиля:
- Для автомобилей, находящихся в неподвижном состоянии, на роль катода подойдет расположенный вблизи металлический объект, например, гараж (при условии, что он построен из металла или имеет металлические элементы), контур заземления, который может быть установлен в отсутствии гаража на открытой стоянке.
- На движущемся автомобиле могут быть использованы такие приспособления, как резиновый металлизированный заземляющийся «хвост», протекторы (защитные электроды), монтируемые на кузов.
Ввиду отсутствия тока, протекающего между электродами, бортовую сеть автомобиля +12 вольт достаточно подключить к одному или нескольким анодам через добавочный резистор. Последнее устройство служит для ограничения тока разряда аккумулятора в случае замыкания анода на катод. Основными причинами замыкания являются неграмотно осуществленная установка оборудования, повреждение анода или его химическое разложение вследствие окисления. Далее рассмотрены особенности применения перечисленных ранее предметов в качестве анодов.
Использование гаража в качестве анода считают наиболее простым способом электрохимической защиты кузова стоящего автомобиля. Если помещение имеет металлический пол или напольное покрытие с открытыми участками железной арматуры, то также будет обеспечена и защита днища. В теплый период в металлических гаражах наблюдается парниковый эффект, однако в случае создания электрохимической защиты он не разрушает автомобиль, а наоборот направлен на защиту его кузова от коррозии.
Создать электрохимическую защиту при наличии металлического гаража весьма просто. Для этого достаточно подключить данный объект к положительному разъему аккумуляторной батареи автомобиля через добавочный резистор и монтажный провод.
В качестве положительного разъема можно использовать даже прикуриватель при условии наличия в нем напряжения при отключенном замке зажигания (не у всех автомобилей данное приспособление сохраняет работоспособность при отключенном двигателе).
Контур заземления при создании электрохимической защиты используют в качестве анода по тому же принципу, что рассмотренный выше металлический гараж. Различие состоит в том, что гараж защищает весь кузов автомобиля, в то время как этот способ - лишь его днище. Контур заземления создают путем забивания в грунт по периметру автомобиля четырех металлических стержней длиной не менее 1 м и натягивания между ними проволоки. Подключение контура к автомобилю, как и гаража, осуществляют через добавочный резистор.
Резиновый металлизированный заземляющий «хвост» является простейшим способом электрохимической защиты движущегося автомобиля от коррозии. Данное приспособление представляет собой резиновую полоску с металлическими элементами. Принцип его функционирования состоит в том, что в условиях высокой влажности между кузовом автомобиля и дорожным покрытием возникает разность потенциалов. Причем чем выше влажность, тем больше эффективность электрохимической защиты, создаваемой рассматриваемым элементом. Заземляющий «хвост» устанавливают в задней части автомобиля таким образом, чтобы на него попадали брызги воды, вылетающие при движении по мокрому дорожному покрытию из под заднего колеса, так как это повышает эффективность электрохимической защиты.
Достоинство заземляющего хвоста состоит в том, что, помимо функции электрохимической защиты, он избавляет кузов автомобиля от статического напряжения. Это особо актуально для транспорта, перевозящего топливо, так как электростатическая искра, являющаяся результатом накопления статического заряда в процессе движения, опасна для транспортируемого им груза. Поэтому приспособления в виде металлических цепей, волочащихся по дорожному покрытию, встречаются, например, на бензовозах.
В любом случае необходимо изолировать заземляющий хвост от кузова автомобиля по постоянному току и наоборот «закоротить» по переменному. Это достигают путем использования RC-цепочки, которая представляет собой элементарный частотный фильтр.
Защита автомобиля от коррозии электрохимическим способом с использованием в качестве анодов защитных электродов рассчитана также на эксплуатацию в движении. Протекторы устанавливают в наиболее уязвимых для коррозии местах кузова, представленных порогами, крыльями, днищем.
Защитные электроды, как и во всех рассмотренных ранее случаях, функционируют по принципу создания разницы потенциалов. Достоинство рассматриваемого способа состоит в постоянном наличии анодов вне зависимости от того, стоит ли автомобиль или движется. Поэтому данную технологию считают весьма эффективной, однако она наиболее сложна в создании. Это объясняется тем, что для обеспечения высокой эффективности защиты необходимо установить на кузове автомобиля 15-20 протекторов.
В качестве защитных электродов могут быть использованы элементы из таких материалов, как алюминий, нержавеющая сталь, магнетит, платина, карбоксил, графит. Первые два варианта относят к разрушающимся, то есть состоящие из них защитные электроды требуется менять с интервалом в 4-5 лет, в то время как остальные называют неразрушающимися, так как они характеризуются значительно большей долговечностью. В любом случае протекторы представляют собой пластины круглой или прямоугольной формы площадью 4-10 см².
В процессе создания такой защиты нужно учитывать некоторые особенности протекторов:
- радиус защитного действия распространяется на 0,25-0,35 м;
- электроды необходимо устанавливать лишь на участки, имеющие лакокрасочное покрытие;
- для закрепления рассматриваемых элементов следует использовать эпоксидный клей или шпатлевку;
- перед установкой рекомендуется зачистить глянец;
- наружную сторону протекторов недопустимо покрывать краской, мастикой, клеем и прочими электроизоляционными веществами;
- так как защитные электроды представляют собой положительно заряженные пластины конденсатора, они должны быть изолированы от отрицательно заряженной поверхности кузова автомобиля.
Роль диэлектрической прокладки конденсатора будет выполнять лакокрасочное покрытие и клей, расположенные между протекторами и кузовом автомобиля. Также нужно учитывать, что величина расстояния между протекторами прямо пропорционально определяет электрическое поле, поэтому их следует устанавливать на небольшом расстоянии друг от друга, чтобы обеспечить достаточную емкость конденсатора.
Провода к защитным электродам подводят через проколы в закрывающих отверстия в днище автомобиля резиновых заглушках. Можно установить на автомобиль много протекторов маленького размера или меньшее количество защитных электродов большего размера. В любом случае необходимо использовать данные элементы на участках, наиболее уязвимых по отношению к коррозии, обращенными наружу, так как роль электролита в данном случае выполняет воздух.
Кузов автомобиля после установки электрохимической защиты такого типа не будет бить током, так как она создает электричество очень небольшой силы. Даже если человек прикоснется к защитному электроду, то не получит удар. Это объясняется тем, что в электрохимической антикоррозийной защите применяется постоянный ток малой силы, создающий слабое электрическое поле. К тому же существует альтернативная теория, согласно которой магнитное поле существует только между поверхностью кузова и местом установки защитных электродов. Поэтому электромагнитное поле, создаваемое электрохимической защитой, более чем в 100 раз слабее электромагнитного поля мобильного телефона.
Протекторная защита является разновидностью катодной защиты. К защищаемой конструкции присоединяют более электроотрицательный металл - протектор - который, растворяясь в окружающей среде, защищает от разрушения основную конструкцию. После полного растворения протектора или потери контакта с защищаемой конструкцией, протектор необходимо заменить.
Протектор работает эффективно, если переходное сопротивление между ним и окружающей средой невелико. Действие протектора ограничивается определенным расстоянием. Максимально возможное удаление его от защищаемой конструкции называется радиусом защитного действия протектора.
Протекторную защиту применяют в тех случаях, когда получение энергии извне для организации катодной защиты связано с трудностями, а сооружение специальных электролиний экономически невыгодно.
Протекторную защиту применяют для борьбы с коррозией металлических конструкций в морской и речной воде, грунте и других нейтральных средах. Использование протекторов в кислых растворах нецелесообразно вследствие высокой скорости саморастворения.
Однако использовать чистые металл в качестве протекторов не всегда целесообразно. Так, например, чистый цинк растворяется неравномерно из-за крупнозернистой дендритной структуры, поверхность чистого алюминия покрывается плотной оксидной пленкой, магний имеет высокую скорость собственной коррозии. Для придания протекторам требуемых эксплуатационных свойств в их состав вводят легирующие элементы.
(от сотых до десятых долей процента), способствующие требуемому изменению параметров решетки. Магниевые протекторные сплавы в качестве легирующих добавок содержат А1 (5-7 %) и Zn (2-5 %); содержание таких примесей, как
Поддерживают на уровне десятых или сотых долей процента. Железо в качестве протекторного материала используют либо в чистом виде (Ре-армко) либо в виде углеродистых сталей.
или оксида цинка 2пО.
Алюминиевые протекторы применяют для защиты сооружений, эксплуатирующихся в проточной морской воде, а также для защиты портовых сооружений и конструкций, располагающихся в прибрежном шельфе.
Магниевые протекторы преимущественно применяют для защиты небольших сооружений в слабоэлектропроводных средах, где эффективность действия алюминиевых и цинковых протекторов низка, - грунтах, пресных или слабосоленых водах. Однако, из-за высокой скорости собственного растворения и склонности к образованию на поверхности труднорастворимых соединений, область эксплуатации магниевых протекторов ограничивается средами с рН = 9,5-10,5. При защите магниевыми протекторами закрытых систем, например резервуаров, необходимо учитывать возможность образования гремучего газа вследствие выделения водорода в катодной реакции, протекающей на поверхности магниевого сплава. Использование магниевых протекторов сопряжено также с опасностью развития водородного охрупчивания и коррозионного растрескивания оборудования.
Любые металлические изделия легко разрушаются под воздействием определенных внешних факторов, чаще всего влажности. Чтобы предотвратить подобные явления, используется протекторная защита от коррозии. Ее задача - снизить потенциал основного материала и тем самым защитить его от коррозии.
Суть процедуры
Протекторная защита строится на основе такого вещества, как ингибитор. Это металл, имеющий повышенные электроотрицательные качества. При воздействии на него воздуха происходит растворение протектора. Вследствие этого основной материал сохраняется, даже если на него оказывается сильное влияние коррозии.
Различные виды коррозии легко победить, если использовать катодные электрохимические методы, к которым относится и протекторная защита. Подобная процедура - идеальное решение, когда у предприятия нет финансовых возможностей или технологического потенциала, чтобы обеспечить полноценную защиту от коррозийных процессов.
Основные преимущества
Протекторная защита металлов от коррозии - это хороший способ защиты любых металлических поверхностей. Использование его целесообразно в нескольких случаях:
- Когда предприятию не хватает производственных мощностей, чтобы использовать более энергозатратные методики.
- Когда требуется защитить малогабаритные конструкции.
- Если требуется защита металлических изделий и объектов, поверхности которых покрыты изоляционными материалами.
Чтобы достичь максимальной эффективности, целесообразно использовать протекторную защиту в электролитической среде.
Когда требуется защита?
Коррозия возникает на любых металлических поверхностях в самых разных сферах - от нефтегазодобывающей промышленности до судостроения. Протекторная защита от коррозии широко применяется в окраске корпусов танкеров. Эти судна постоянно подвергаются воздействию воды, и специальная окраска не всегда справляется с предотвращением реакций влаги с металлической поверхностью. Использование протекторов - простое и эффективное решение проблемы, особенно если суда будут находиться в эксплуатации длительное время.
Большинство конструкций из металла создается из стали, поэтому целесообразно использовать протекторы, имеющие отрицательный электродный потенциал. Основными для производства протекторов являются три металла - цинк, магний, алюминий. Из-за большой разности потенциалов этих металлов и стали радиус защитного действия становится шире, и любые виды коррозии легко устраняются.
Какие металлы используются?
Защитная система строится на основе различных сплавов, в зависимости от специфики использования протекторов, например, среды, в которой он будет использоваться. Протекторная защита от коррозии чаще всего требуется железным и стальным изделиям, но и поверхностям из цинка, алюминия, кадмия или магния она также требуется. Особенность протекторной защиты - в использовании гальванических анодов, которые обеспечивают защиту труб от почвенной коррозии. Расчет подобных установок выполняется с учетом ряда параметров:
- силы тока в протекторе;
- показателей его сопротивления;
- степени защиты, нужной для 1 км трубы;
- количества протекторов на этот же отрезок;
- расстояния, которое имеется между элементами защитной системы.
Плюсы и минусы различных протекторов
На основе протекторов строится защита строительных конструкций от коррозии, трубопроводов разного типа (распределительных, магистральных, промысловых). При этом использовать их нужно грамотно:
- использование алюминиевых протекторов целесообразно для того, чтобы защитить конструкции и сооружения в морской воде и прибрежном шельфе;
- магниевые подходят для использования в слабоэлектропроводной среде, где алюминиевые и цинковые протекторы показывают низкую эффективность. Но их нельзя использовать, если требуется защитить внутренние поверхности танкеров, резервуаров, отстойников для нефти, так как магниевые протекторы отличаются повышенной взрыво- и пожароопасностью. В идеале проекторы на основе этого элемента нужно использовать для внешней защиты конструкций, которые используются в пресной среде;
- цинковые протекторы полностью безопасны, поэтому их можно использовать на любых объектах, даже если на них высокий уровень пожарной опасности.
Если покрытие лакокрасочное
Очень часто требуется обеспечить защиту нефте- или газопровода от коррозии с учетом лакокрасочного покрытия. Комбинация его с протектором - это пассивный способ защиты конструкций от коррозии. При этом эффективность такого мероприятия не так высока, зато достигается следующее:
- нивелируются дефекты на покрытиях конструкций из металлов, трубопроводов, например, отслаивание, появление трещин;
- снижается расход протекторных материалов, при этом сама защита оказывается более долговечной;
- защитный ток равномерно распределяется по металлической поверхности изделия или объекта.
Протекторная защита от коррозии в сочетании с лакокрасочными покрытиями - это возможность распределения защитного тока именно на те поверхности, которые требуют максимального внимания.
О защите трубопроводов
По мере эксплуатации металлические трубы изнутри и снаружи подвергаются воздействию коррозии. Налет появляется вследствие того, что по трубам текут агрессивные вещества, которые вступают в реакцию с материалами. На внутреннее состояние металлических изделий влияет высокий уровень влажности почвы. Если не будет продумана качественная защита строительных конструкций от коррозии, произойдет следующее:
- трубопровод начнет разрушаться изнутри;
- потребуется чаще проводить профилактические осмотры магистралей;
- потребуется более частый ремонт, что скажется на дополнительных тратах;
- потребуется полностью или частично остановить нефтеперерабатывающий или иной другой промышленный комплекс.
Существует несколько способов защиты трубопроводов - пассивные, активные. Также как средство защиты может выступать снижение агрессивности среды. Чтобы защита была комплексной, учитывается тип трубопровода, способ его монтажа и взаимодействие с окружающей средой.
Пассивные и активные методы защиты
Все основные способы защиты трубопроводов от коррозии сводятся к выполнению целого ряда работ. Если говорить о пассивных методах, они выражаются в следующем:
- особом способе укладки, когда сопротивляемость к коррозии продумывается еще на стадии монтажа трубопровода. Для этого между землей и трубой оставляется воздушный зазор, благодаря которому внутрь трубопровода не попадут ни грунтовые воды, ни соли, ни щелочи;
- нанесении специальных покрытий на трубы, которые будут защищать поверхность от почвенных воздействий;
- обработке специальной химией, например, фосфатами, образующими на поверхности защитную пленку.
Схема защиты на основе активных методов предполагает использование электрического тока и электрохимических реакций ионного обмена:
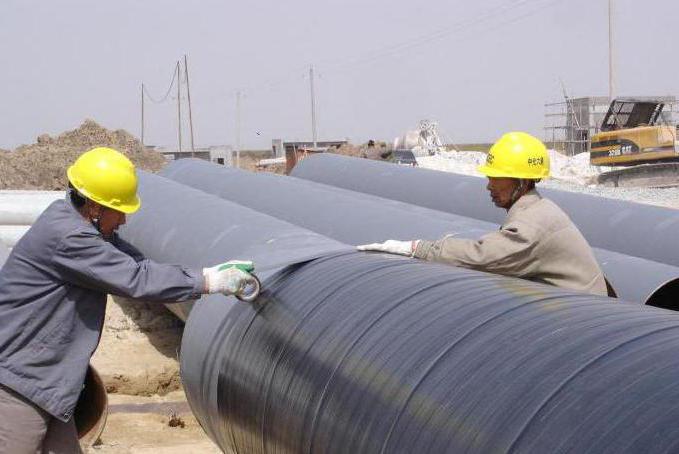
Доводы в пользу протекторной защиты
Как видно, способов повысить защитные характеристики трубопроводов и других металлических изделий немало. Но все они требуют траты электрического тока. Протекторная защита от коррозии трубопроводов - более выгодное решение, так как все процессы окислов прекращаются просто нанесением на поверхности труб из металлов сплавов других материалов. В пользу такого способа говорят следующие факторы:
- экономичность и простота процесса за счет отсутствия источника постоянного тока и применения сплавов магния, цинка или алюминия;
- возможность применения одиночных или групповых установок, при этом схема протекторной защиты продумывается с учетом особенностей проектируемого или уже построенного объекта;
- возможность применения на любых почвах и в условиях морей/океанов, где дорого или невозможно использовать источники внешнего тока.
Протекторную защиту можно использовать для повышения сопротивляемости коррозии различных резервуаров, корпусов судов, цистерн, которые используются в экстремальных условиях.
3.1 Катодная защита
Катодная защита - наиболее распространенный вид электрохимической защиты. Она применяется в тех случаях, когда металл не склонен к пассивации, то есть имеет протяжненную область активного растворения, узкую пассивную область, высокие значения тока пассивации (i п) и потенциала пассивации (φ п).
Катодную поляризацию можно осуществлять путем присоединения защищаемой конструкции к отрицательному полюсу внешнего источника тока или к металлу, имеющему более электроотрицательный электродный потенциал. В последнем случае нет надобности во внешнем источнике тока, так как образуется гальванический элемент с тем же направлением тока, т. е. защищаемая деталь становится катодом, а более электроотрицатель-ный металл, называемый протектором , - анодом.
Катодная защита внешним током. Катодную защиту с использованием поляризации от внешнего ис-точника тока применяют для защиты оборудования из углеродистых, низко- и высоколегированных и высокохромистых сталей, олова, цинка, медных и медно-никелевых сплавов, алюминия и его сплавов, свинца, титана и его сплавов. Как правило, это подземные соору-жения (трубопроводы и кабели различных назначений, фундаменты, буровое оборудование), оборудование, эксплуатируемое в контакте с морской водой (корпуса судов, металлические части береговых сооружений, морских буровых платформ), внутренние поверхности аппаратов и резервуаров химической промышленности. Часто ка-тодную защиту применяют одновременно с нанесением защитных покрытий. Уменьшение скорости саморастворения металла при его внешней поляризации называют защитным эффектом. Основным критерием катодной защиты является защитный по-тенциал. Защитным потенциалом называется потенциал, при ко-тором скорость растворения металла принимает предельно низкое значение, допустимое для данных условий эксплуатации. Харак-теристикой катодной защиты является величина защитного эффек-та Z, %:Где K 0 [г/(м 2 ·ч)] - скорость коррозии металла без защиты, К 1 [г/(м 2 ·ч)] - скорость коррозии металла в условиях электрохимической защиты. Коэффициент защитного действия К 3 [г/А] определяют по формуле
К 3 = (m 0 - m i)/i K ,
Где m o и m i - потери массы металла соответственно без ка-тодной защиты и при ее применении, г/м 2 ; i к [А/м 2 ] - плотность катодного тока. Схема катодной защиты представлена на рис. 51. Отрицательный полюс внешнего источника тока 4 присоединен к защищаемой металлической конструкции 1, а положительный полюс – к вспомогательному электроду 2, работающему как анод. В процессе защиты анод ак-тивно разрушается и подлежит периодическому восста-новлению.
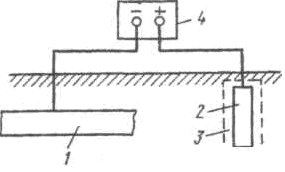
Рисунок 53 - Схема протекторной защиты трубопровода Протектор работает эффективно, если переходное сопротивление между ним и окружающей средой неве-лико. В процессе работы протектор, например цинковый, может покрываться слоем нерастворимых продуктов коррозии, которые изолируют его от окружающей среды и резко увеличивают переходное сопротивление. Для борьбы с этим протектор помещают в наполнитель 4
- смесь солей, которая создает вокруг него определен-ную среду, облегчающую растворение продуктов коррозии и повышающую эффективность и стабильность работы протектора в грунте 1. Действие протектора ограничивается определенным расстоянием. Максимально возможное удаление проте-ктора от защищаемой конструкции называется радиусом действия протектора. Он зависит от ряда факторов, важнейшими из которых являются электропроводность среды, разность потенциалов между протектором и за-щищаемой конструкцией, поляризационные характерис-тики. С увеличением электропроводности среды защит-ное действие протектора распространяется на большее расстояние. Так, радиус действия цинкового про-тектора при защите стали в дистиллированной воде равен 0,1см, морской воде 4 м, в 3% растворе NaCl - 6
м. Протекторную защиту по сравнению с катодной за-щитой внешним током целесообразно использовать в тех случаях, когда получение энергии извне связано с трудностями или если сооружение специальных электро-линий экономически невыгодно. В настоящее время протекторную защиту применяют для борьбы с коррозией металлических конструкций
в морской и речной воде, грунте и других нейтральных
средах. Использование протекторной защиты в кислых
средах ограничивается высокой скоростью саморастворения протектора. В качестве протекторов можно применять металлы: Al, Fe, Mg, Zn. Однако использовать чистые металлы в качестве протекторов не всегда целесообразно. Так, например, чистый цинк растворяет-ся неравномерно из-за крупнозернистой дендритной структуры, по-верхность чистого алюминия покрывается плотной оксидной плен-кой, магний имеет высокую скорость собственной коррозии. Для придания протекторам требуемых эксплуатационных свойств в их состав вводят легирующие элементы. В состав цинковых протекторов вводят Cd (0,025-0,15%) и А1 (0,1-0,5%). Содержание таких примесей, как Fe, Cu, Pb, стараются поддерживать на уровне не более 0,001-0,005 %. В состав алюмини-евых протекторов вводят добавки, предотвращающие образование оксидных слоев на их поверхности - Zn (до 8 %), Mg (до 5 %), а также Cd, In, Gl, Hg, Tl, Mn, Si (от сотых до десятых долей процен-та), способствующие требуемому изменению параметров решетки. Магниевые протекторные сплавы в качестве легирующих добавок содержат Al
(5-7 %) и Zn (2-5 %); содержание таких примесей, как Fe, Ni, Cu, Pb, Si поддерживают на уровне десятых или сотых долей процента. Железо в качестве протекторного материала используют либо в чистом виде (Fe-армко), либо в виде углеродистых сталей. Цинковые протекторы применяют для защиты оборудования, экс-плуатирующегося в морской воде (морских судов, трубопроводов, прибрежных сооружений). Применение их в слабосоленой, пресной воде и грунтах ограничено вследствие образования на их поверхно-сти слоев гидроксида Zn(OH) 2 или оксида цинка ZnO. Алюминиевые протекторы применяют для защиты сооружений, эксплуатирующихся в проточной морской воде, а также для защиты портовых сооружений и конструкций, располагающихся в прибреж-ном шельфе. Магниевые протекторы преимущественно применяют для защиты небольших сооружений в слабоэлектропроводных средах, где эф-фективность действия алюминиевых и цинковых протекторов низка, - грунтах, пресных или слабосоленых водах. Однако из-за высокой скорости собственного растворения и склонности к образованию на поверхности труднорастворимых соединений область эксплуатации магниевых протекторов ограничивается средами с рН = 9,5 – 10,5. При защите магниевыми протекторами закрытых систем, напри-мер резервуаров, необходимо учитывать возможность образования гремучего газа вследствие выделения водорода в катодной реакции, протекающей на поверхности магниевого сплава. Использование магниевых протекторов сопряжено также с опасностью развития водородного охрупчивания и коррозионного растрескивания обору-дования. Как и в случае катодной защиты внешним током, эффективность протекторной защиты возрастает при ее совместном использовании с защитными покрытиями. Так, нанесение битумного покрытия на трубопроводы значительно улучшает распределение защитного тока, уменьшает число анодов и увеличивает протяженность участка трубопровода, защищаемого с помощью одного протектора. Если одним магниевым анодом можно обеспечить защиту непокрытого трубопровода длиной всего 30 м, то защита покрытого битумом трубопровода действует на длину до 8 км.
3.2 Анодная защита
Анодную защиту применяют при эксплуатации оборудования в хорошо электропроводных средах и изготовленного из легко пассивирующихся материалов – углеродистых, низколегированных нержавеющих сталей, титана, высоколегированных сплавов на основе железа. Анодная защита перспективна в случае оборудования, изготовленного из разнородных пассивирующихся материалов, например нержавеющих сталей различного состава, сварных соединений. Анодная защита осуществляется присоединением защищаемой металлической конструкции к положительному полюсу внешнего источника постоянного тока или к металлу с более положительным потенциалом (катодный протектор).При этом потенциал защищаемого металла смещается в положительную сторону до достижения устойчивого пассивного состояния (рис. 50). В результате происходит не только существенное (в тысячи раз) снижение скорости коррозии металла, но и предотвращение попадания продуктов его растворения в производимый продукт. Катоды, используемые при анодной защите от внешнего источника тока, должны иметь высокую устойчивость в коррозионной среде. Выбор материала катода определяется характеристиками среды. Используют такие материалы, как Pt, Ta, Pb, Ni, платинированную латунь, высоколегированные нержавеющие стали и др. Схема расположения катодов проектируется индивидуально для каждого конкретного случая защиты. В качестве катодного проектора можно использовать такие материалы, как углерод, диоксид марганца, магнетит, диоксид свинца, имеющие весьма положительный потенциал. Анодная защита от внешнего источника основана на пропускании тока через защищаемый объект и на смещении потенциала коррозии в сторону более положительных значений. Установка для анодной защиты состоит из объекта защиты, като-да, электрода сравнения и источника электрического тока. Основным условием возможности применения анодной защи-ты является наличие протяженной области устойчивой пассивности металла при плотности тока растворения металла не более (1,5- 6,0)·10 -1 А/м 2 . Основным критерием, характеризующим состояние поверхности металла, является электродный потенциал. Обычно возможность применения анодной защиты для конкретного металла или спла-ва определяют методом снятия анодных поляризационных кривых. При этом получают следующие данные: а) потенциал коррозии металла в исследуемом растворе; б) протяженность области устойчивой пассивности; в) плотность тока в области устойчивой пассивности. Эффективность защиты определяют как отношение скорости кор-розии без защиты к скорости коррозии под защитой. Как правило, параметры анодной защиты, полученные в лабора-торных и производственных условиях, хорошо согласуются между собой. В зависимости от конкретных условий эксплуатации область защитных потенциалов при анодной защите лежит на 0,3-1,5В положительнее потенциала свободной коррозии, а скорость растворения металлов при этом может уменьшиться в тысячи раз. Существенным ограничением применения анодной защиты яв-ляется вероятность возникновения локальных видов коррозии в об-ласти пассивного состояния металла. Для предотвращения этого яв-ления на основании предварительных исследований рекомендуют такое значение защитного потенциала, при котором локальные виды коррозии не возникают или в раствор вводят ингибирующие добав-ки. Например, анодная защита стали 12X18Н10Т в растворах хлори-дов в присутствии ионов N0 3 - предотвращает образование питтингов и снижает скорость растворения стали в 2000 раз. В ряде случаев вследствие повышенной опасности возникновения локальных кор-розионных процессов применение анодной защиты неэффективно. Резкий рост тока пассивации металлов с увеличением температуры агрессивных сред ограничивает применение анодной защиты в условиях повышенных температур. При стационарном режиме работы установки величина тока поляризации, требуемого для поддержания устойчивого пассивного состояния, постоянно меняется вследствие изменения эксплуатаци-онных параметров коррозионной среды (температуры, химическо-го состава, условий перемешивания, скорости движения раствора и др.). Поддерживать потенциал металлоконструкции в заданных гра-ницах можно путем постоянной или периодической поляризации. В случае периодической поляризации включение и выключение тока производят либо при достижении определенного значения потенци-ала, либо при его отклонении на определенную величину. В обоих случаях параметры анодной защиты определяют опытным способом в лабораторных условиях. Для успешного применения анодной защиты объект должен от-вечать следующим требованиям: а) материал аппарата должен пассивироваться в технологической среде; б) конструкция аппарата не должна иметь заклепок, количество щелей и воздушных карманов должно быть минимальным, свар-ка должна быть качественной; в) катод и электрод сравнения в защищаемом устройстве должны постоянно находиться в растворе. В химической промышленности для анодной защиты наиболее пригодны аппараты цилиндрической формы, а также теплообменни-ки. В настоящее время анодная защита нержавеющих сталей при-меняется для мерников, сборников, цистерн, хранилищ в производ-стве серной кислоты, минеральных удобрений, аммиачных раство-ров. Описаны случаи применения анодной защиты теплообменной аппаратуры впроизводствах серной кислоты и искусственного во-локна, а также ванн для химического никелирования. Метод анодной защиты имеет относительно ограниченное применение, так как пассивация эффективна в основном в окислительных средах при отсутствии активных депассивирующих ионов, например ионов хлора для железа и нержавеющих сталей. Кроме того, анодная защита потенциально опасна: в случае переры-ва подачи тока возможно активирование металла и его интенсивное анодное растворение. Поэтому анодная защита требует наличия тщательной системы контроля. В отличие от катодной защиты скорость коррозии при анодной защите никогда не уменьшается до нуля, хотя может быть и очень небольшой. Зато защитная плотность тока здесь значительно ниже, а потребление электроэнергии невелико. Другое достоинство анодной защиты - высокая рас-сеивающая способность, т.е. возможность защиты на более отдаленном от катода расстоянии и в электрически экранированных участках.3.3 Кислородная защита
Кислородная защита является разновидностью электрохимиче-ской защиты, при которой смещение потенциала защищаемой ме-таллоконструкции в положительную сторону осуществляется путем насыщения коррозионной среды кислородом. В результате этого ско-рость катодного процесса настолько возрастает, что становится воз-можным перевод стали из активного в пассивное состояние.Рисунок 54 - Зависимость скорости коррозии низколегированной стали в воде при тем-пературе 300 °С от концентрации кислорода в воде По-скольку величина критиче-ского тока пассивации спла-вов Fe-Cr, к которым относятся и стали, существенно зависит от содержания в них хрома, ее эффективность возрастает с увеличением концентрации хрома в сплаве. Кислородная защита применяется при коррозии тепло-энергетического оборудова-ния, эксплуатирующегося в воде при высоких парамет-рах (высокие температура и давление). На рис. 54 представлена зависимость скорости коррозии низколегированной стали от концентрации кислорода в высокотем-пературной воде. Как видно, увеличение концентрации растворен-ного в воде кислорода приводит к первоначальному росту скорости коррозии, последующему се снижению и дальнейшей стационарности. Низкие стационарные скорости растворения стали (в 10-30 раз ниже имеющих место без защиты) достигаются при содержании кислорода в воде ~ 1,8 г/л. Кислородная защита металлов нашла применение в атомной энергетике.
4. Разработка и производство новых
конструкционных материалов повышенной коррозионной устойчивости
Улучшение антикоррозионных свойств самих металлических материалов осуществляется:
- устранением из металлов и сплавов примесей, ускоряющих коррозионные процессы; легированием.
5 Переход в ряде конструкций от металлических
к химически стойким неметаллическим материалам
Дополнительным резервом для организации противокоррозионной защиты являются неметаллические материалы. Из стекла, керамики, ситаллов, винипласта, фаолита, графита и других неметаллических материалов могут быть изготовлены отдельные аппараты или детали к ним. Их отличительной особенностью является высокая коррозионная стойкость во многих агрессивных средах. Подробно неметаллические материалы рассмотрены в главе V, часть 4.
6 Рациональное конструирование и эксплуатация металлических сооружений и деталей
При проектировании химического производства, как правило, уделяют основное внимание анализу характера агрессивной среды и условиям протекания процесса. Руководствуясь этими данными, выбирают материал, обладающий достаточным химическим сопротивлением. Однако конструкционный материал,наиболее стойкий в данной коррозионной среде, далеко не во всех случаях позволяет предотвращать опасность быстрого коррозионного разрушения. Поэтому столь же пристального внимания заслуживает рациональное конструирование отдельных узлов и аппаратов. Неудачное конструирование во многих случаях может явиться причиной образования застойных зон, зазоров, концентрации напряжений и других явлений, способствующих возникновению и протеканию коррозии. Вместе с тем уже на стадии проектирования можно предусмотреть такие конструктивные решения отдельных узлов аппарата, которые значительно снизят или устранят возможность возникновения процесса коррозии. При конструировании оборудования следует обращать внимание на характер обработки поверхности металла, контакт соединительных элементов из различных материалов, режим распределения потоков теплоносителя, наличие щелей и зазоров, возможность образования застойных зон. Гладкая поверхность металла имеет меньше дефектов в виде царапин, неровностей и т.д. На шероховатой поверхности легче скапливаются грязь, пыль и другие вещества. Это особенно характерно для производства удобрений, солей. Металлическое оборудование и конструкции с шероховатой поверхностью в этом случае покрываются различными веществами. Если эти вещества гигроскопичны, то они прилипают к поверхности металла, создаются местные очаги с высокой концентрацией электролита, что способствует усилению коррозии. Если в конструируемом аппарате есть детали, выполненные из различных металлических материалов, то возникает опасность появления контактной коррозии . В этом случае еще на стадии проектирования обязательно должны быть приняты меры по предотвращению или ослаблению этого явления. Обычно применяют один из двух возможных приемов. Контактирующие детали из разнородных металлов изготавливают с различной величиной поверхности. При этом деталь с наименьшей поверхностью должна быть выполнена из более благородного металла (втулки вентилей, поршневые кольца насосов и т.д.). Если такой способ оказывается невозможным, то детали из разных материалов изолируют друг от друга. Особое внимание при этом следует уделить свойствам прокладочного материала. Он должен быть инертным по отношению к рабочей среде, иметь высокую износостойкость. Некоторые изоляционные материалы (войлок, асбест, древесина) могут впитывать и удерживать влагу и, таким образом, быть очагами усиления коррозии. Некоторые полимерные материалы, подвергаясь со временем старению, при соприкосновении с водой могут выделять коррозионноактивные агенты, ускоряющие разрушение металлов. Поэтому изоляционные материалы часто пропитывают дегтем или битумом, а применяемые полимерные материалы подвергают специальным исследованиям с целью определения опасности выделения агрессивных агентов. Многие процессы протекают при повышенных температурах. Поверхность металла, соприкасающаяся с теплоносителями, подвергается дополнительному коррозионному воздействию. Чем выше температура, тем интенсивнее происходит разрушение металла. Например, теплообменники являются одним из наименее стойких видов оборудования. В 92% случаев причиной отказа в работе теплообменников является коррозия теплоотдающих поверхностей. При проектировании аппаратов следует предусмотреть равномерное распределение теплового потока, исключить возможность локального перегрева. Во многих промышленных аппаратах, в которых протекают высокотемпературные процессы, такие меры предусмотрены. Например, в производстве аммиака между катализаторной коробкой, в которой осуществляется реакция при температуре 350-420ºС, и корпусом аппарата предусмотрен канал, внутри которого циркулируется холодный газ. Таким конструктивным приемом предохраняют стенки аппарата от перегрева. Если в химическом процессе используют реакторы с рубашкой, то внутри реактора должна быть установлена мешалка для обеспечения равномерного перемещения жидкости мимо теплопередающей поверхности. Змеевики, кипятильники и другое оборудование для нагрева технологических сред должны быть погружены в жидкость. Для теплообменного оборудования наиболее распространенными являются локальные виды коррозии, такие, как питтинговая, щелевая, межкристаллитная. При проектировании конструкций должны быть обозначены места и способы сварки. При сварке металлов в зоне шва и околошовной зоне создаются большие растягивающие напряжения. В зонах, расположенных вдоль шва, где металл нагревается выше критических температур, меняется структура металла. Это может привести к растрескиванию металла. При конструировании сварных узлов и деталей следует предусмотреть ряд мер: избегать скопления швов, исключить точечную сварку, при которой особенно велика концентрация напряжений, применять местный отжиг и т.д. Скопление влаги в различных элементах конструкции способствует развитию коррозии. Поэтому при создании различных конструкций предусматривают возможность проветривания полостей, наличие дренажных отверстий и др. Очень опасными в коррозионном отношении зонами в аппаратуре являются зазоры и щели. В них может происходить концентрирование рабочего раствора, нарушается аэрация, что неизбежно приведет к развитию местной коррозии. С этой точки зрения опасны прерывистые, сварные швы, в которых вследствие неплотного прилегания материала друг к другу образуются щели и зазоры, являющиеся причиной возникновения щелевой коррозии. Образование застойных зон жидкости в аппаратах и трубопроводах сильно увеличивает возможность возникновения коррозии за счет образования микропара неравномерной аэрации. Этому способствует и отложение различных осадков в застойной зоне. На изделии не должно быть различных углублений, канавок и пазов, в которых может скапливаться влага. Элементы конструкции должны быть по возможности обтекаемыми, это облегчает испарение влаги. В рационально сконструированных узлах устранена возможность скапливания влаги и продуктов коррозии, предусмотрена возможность удаления осадка. Существуют и другие требования к конструированию, обеспечивающие создание изделий, в наименьшей степени подверженных опасности развития коррозии. К ним относятся: требования к общей компоновке и расположению элементов, учет возможности нанесения и возобновления различных покрытий в процессе эксплуатации и при ремонте, учет особенностей эксплуатации изделий и др.
СПИСОК ЛИТЕРАТУРЫ
Анодная защита. Использование пассивности в практике защиты от коррозии.
Многие металлы находятся в пассивном состоянии в некоторых агрессивных средах. Хром, никель, титан, цирконий легко переходят в пассивное состояние и устойчиво его сохраняют. Часто легирование металла, менее склонного к пассивации, металлом, пассивирующем легче, приводит к образованию достаточно хорошо пассивирующихся сплавов. Примером могут служить разновидности сплавов Fе-Сr, представляющие собой различные нержавеющие и кислотоупорные стали, стойкие, например, в пресной воде, атмосфере, азотной кислоте и т.д. Подобное использование пассивности в технике защиты от коррозии известно давно и имеет огромное практическое значение. Но в последнее время возникло новое направление защиты металлов в таких окислителях, которые сами по себе не способны вызывать пассивность. Известно, что смещение потенциала активного металла в отрицательную сторону должно уменьшить скорость коррозии. Если потенциал становится отрицательнее равновесного в данной среде, то скорость коррозии должна стать равной нулю (катодная защита, применение протекторов). Очевидно, что подобным же образом, но за счет анодной поляризации от внешнего источника электрической энергии можно перевести способный к этому металл в пассивное состояние и тем уменьшить скорость коррозии на несколько порядков. Расход электрической энергии не должен быть велик, так как сила тока вообще весьма мала. Существуют требования, которым должна удовлетворять система, чтобы к ней можно было применить анодную защиту. Прежде всего, нужно надежно знать анодную поляризационную кривую для выбранного металла в данной агрессивной среде. Чем выше i п , тем большая сила тока потребуется для перевода металла в пассивное состояние; чем меньше i nn , тем меньший расход энергии потребуется для поддержания пассивности; чем шире диапазон Δφ n , тем большие колебания потенциала можно допустить, т.е. тем легче поддерживать металл в пассивном состоянии. Нужна уверенность в том, что в области Δφ n металл корродирует равномерно. В противном случае, даже при малой величине i nn возможно образование язв и сквозного разъедания стенки изделия. Форма защищаемой поверхности может быть довольно сложной, что затрудняет поддержание одинакового значения потенциала на всей поверхности; в этом отношении большая величина Δφ n особенно желательна. Конечно, требуется и достаточно хорошая электропроводность среды. Применение анодной защиты целесообразно в сильно агрессивных средах, например в химической промышленности. При наличие поверхности раздела жидкость-газ необходимо иметь в виду, что анодная защита не может распространяться на поверхность металла в газовой среде, что впрочем типично и для катодной зашиты. Если газовая фаза тоже агрессивна или имеется неспокойная поверхность раздела, что приводит к разбрызгиванию жидкости и оседанию капель ее на металл выше поверхности раздела, если происходит периодическое смачивание стенки изделия в определенной зоне, то приходится ставить вопрос об иных способах защиты поверхности выше постоянного уровня жидкости. Анодная защита может осуществляться несколькими способами. 1. Простое наложение постоянной э.д.с. от постороннего источника электрической энергии. Положительный полюс подключается к защищаемому изделию, а около его поверхности помещают катоды сравнительно малого размера. Они размещаются в таком количестве и на таком расстоянии от защищаемой поверхности, чтобы обеспечить по возможности равномерную анодную поляризацию изделия. Этот способ применяется в том случае, если Δφ n достаточно велик и нет опасности, при некоторой неизбежной неравномерности распределения потенциала анода, активации или перепассивации, т.е. выхода за пределы Δφ n . Таким способом можно защищать изделия из титана или циркония в серной кислоте. Нужно только помнить, что для пассивации сначала потребуется пропускание тока большей силы, что связано с переводом потенциала за φ n . Для начального периода целесообразно иметь дополнительный источник энергии. Следует учитывать также большую поляризацию катодов, плотность тока на которых велика вследствие их малых размеров. Однако, если область пассивного состояния велика, то изменение потенциала катода даже на несколько десятых вольта не представляет опасности. Периодическое включение и выключение тока защиты, когда изделие уже запассивировано. При включение анодного тока потенциал изделия смещается в отрицательную сторону, причем может произойти депассивация. Но поскольку иногда это происходит довольно медленно, простая автоматика может обеспечить включение и выключение защитного тока в нужное время. Когда потенциал дойдет до величины φ nn ", т.е. до начала перепассивации, ток выключается; когда потенциал сдвинется в отрицательную сторону до φ nn (начало активации), ток снова включается. Смещение потенциала в катодную сторону происходит тем медленнее, чем меньше φ nn . Чем ближе был потенциал к величине φ nn ", тем медленнее он смещается в отрицательную сторону (в направлении φ nn) при выключении тока. Например, для хрома в 0,1н. растворе Н 2 SО 4 при 75°С, если выключение тока произошло при φ =0,35в, активация наступит через 2 ч; выключение тока при φ =0,6в вызывает активацию через 5 ч; выключение же при φ =1,05в увеличивает срок начала активации более чем до 127 ч. Столь большое время, необходимое для депассивации, позволяет делать значительные перерывы в подаче тока. Тогда одной и той же установкой можно обслужить несколько объектов. Зависимость времени запассивации от потенциала включения легко объяснима при помощи концепции фазового окисла (образуется более толстый слой окисла, растворение которого требует больше времени). Труднее объяснить это явление десорбцией пассивирующего кислорода. Конечно, с ростом положительного значения потенциалапрочность связи в адсорбционном слое должна увеличиваться. Но при включении тока разряд двойного слоя происходит сравнительно быстро, хотя адсорбционный слой, возможно, сохраняется долго. 3. Если область пассивного состояния (Δφ nn) мала, то необходимо применение потенциостата, поддерживающего заданную величину потенциала (относительно некоторого электрода сравнения) в узких границах. Потенциостат должен быть способен давать большую силу тока. В настоящее время уже имеется ряд установок для анодной защиты, осуществленных в промышленном масштабе. Защищаются изделия и из обычной углеродистой стали. При анодной защите не только увеличивается срок службы аппаратуры, но также уменьшается загрязнение агрессивной среды продуктами коррозии. Например, в олеуме углеродистая сталь корродирует очень медленно и в этом смысле не нуждается в защите. Но в сосудах для хранения этого продукта происходит загрязнение его железом. Так, без анодной защиты в одной из промышленных установок содержание железа в олеуме составляло ~ 0,12 %. После наложения защиты концентрация железа снизилась до ~ 0,004 %, что соответствует его содержанию в исходном продукте. Загрязнение продуктов химической промышленности примесями соединений металлов, являющееся следствием коррозии аппаратуры, во многих случаях весьма нежелательно и даже недопустимо. Однако, использование анодной защиты связано со значительными трудностями. В то время как катодная защита может употребляться для защиты многих металлов, погруженных в любую электропроводящую среду, например твердую или жидкую, анодная защита применяется только для защиты целых секций химических установок, которые изготовлены из металла, способного пассивироваться в рабочей среде. Именно это и ограничивает ее применение. Кроме того, анодная защита потенциально опасна, поскольку при перерывах подачи тока без немедленного восстановления защиты на рассматриваемом участке начнется очень быстрое растворение, так как разрыв в пленке образует путь с низким сопротивлением в условиях анодной поляризации металла. Использование анодной защиты требует тщательного проектирования химической установки. Последняя должна иметь такую систему контроля, чтобы любая потеря защиты немедленно привлекала внимание оператора. Для этого может быть достаточным только локальное повышение анодного тока, однако в наихудшем случае может потребоваться немедленное опорожнение всей установки. Анодная защита не обеспечивает стойкости в присутствии агрессивных ионов. Так, хлоридные ионы разрушают пассивную пленку, а потому их концентрация должна поддерживаться низкой, за исключением защиты титана, который может пассивироваться в хлористоводородной кислоте. В условиях анодной защиты имеет место хорошая рассеивающая способность электролитов и поэтому для поддержания ее установленнойзащиты требуется сравнительно небольшое количество электродов. Однако при проектировании установок анодной защиты следует учитывать, что в условиях, предшествующих пассивации, рассеивающая способность хуже. Анодная защита потребляет очень мало энергии и может применяться для защиты обычных конструкционных металлов, способных пассивироваться, например углеродистой и нержавеющей стали, во многих средах. Эта защита легко подвергается контролю и измерениям и не требует дорогостоящей обработки поверхности металла, так как использует самопроизвольный эффект реакции между стенками емкостей и их содержимым. Способ изящен, и его применение, по-видимому, будет расширяться, как только будут преодолены сложности измерения и контроля.Покрытия, как метод защиты металлов от коррозии.
Защита металлов, основанная на изменение их свойств, осуществляется или специальной обработкой их поверхности, или легированием. Обработка поверхности металла с целью уменьшения коррозии проводится одним из следующих способов: покрытием металла поверхностными пассивирующими пленками из его трудно растворимых соединений (окислы, фосфаты, сульфаты, вольфраматы или их комбинации), созданием защитных слоев из смазок, битумов, красок, эмалей и т.п. и нанесением покрытий из других металлов, более стойких в данных конкретных условиях, чем защищаемый металл (лужение, цинкование, меднение, никелирование, хромирование, свинцование, родирование и т.д.). Защитное действие большинства поверхностных пленок можно отнести за счет вызванной ими механической изоляции металла от окружающей среды. По теории локальных элементов, их эффект следует рассматривать как результат увеличения электрического сопротивления (рис. 8). Повышение устойчивости железных и стальных изделий при покрытии их поверхности осадками других металлов обусловлено и механической изоляцией поверхности, и изменением ее электрохимических свойств. При этом может наблюдаться или смещение обратимого потенциала анодной реакции в сторону более положительных значений (покрытия медью, никелем, родием), или увеличение поляризации катодной реакции - повышение водородного перенапряжения (цинк, олово, свинец). Как следует из диаграмм, все эти изменения уменьшают скорость коррозии. Обработку поверхности металлов применяют для предохранения машин, оборудования, аппаратов и предметов домашнего обихода при временной защите в условиях транспортировки, хранения и консервации (смазка, пассивирующие пленки) и для более длительной защиты при их эксплуатации (лаки, краски, эмали, металлические покрытия). Общим недостатком этих металлов является то, что при удалении (например, вследствие износа или повреждения) поверхностного слоя скорость коррозии на поврежденном месте резко возрастает, а повторное нанесение защитного покрытия не всегда бывает возможно. В этом отношении легирование является значительно более эффективным (хотя и более дорогим) методом повышения коррозионной стойкости металлов. Примером повышения коррозийной стойкости металла легированием являются сплавы меди с золотом. Для надежной защиты меди необходимо добавлять к ней значительное количество золота (не менее 52,2 ат.%). Атомы золота механически защищают атомы меди от их взаимодействия с окружающей средой. Несравненно меньше количество легирующих компонентов требуется для повышения устойчивости металла, если эти компоненты способны образовывать с кислородом защитные пассивирующие пленки. Так, введение хрома в количестве нескольких процентов резко увеличивает коррозионную стойкостьИнгибиторы.
Скорость коррозии можно снизить также изменением свойств коррозионной среды. Это достигается или соответствующей обработкой среды, в результате которой уменьшается ее агрессивность, или введением в коррозионную среду небольших добавок специальных веществ, так называемых замедлителей или ингибиторов коррозии. Обработка среды включает в себя все способы, уменьшающие концентрацию ее компонентов, особенно опасных в коррозионном отношении. Так, например, в нейтральных солевых средах и пресной воде одним из самых агрессивных компонентов является кислород. Его удаляют деаэрацией (кипячение, дистилляция, барботаж инертного газа) или смазывают при помощи соответствующих реагентов (сульфиты, гидразин и т.п.). Уменьшение концентрации кислорода должно почти линейно снижать предельный ток его восстановления, а следовательно, и скорость коррозии металла. Агрессивность среды уменьшается также при ее подщелачивании, снижение общего содержания солей и замене более агрессивных ионов менее агрессивными. При противокоррозионной подготовке воды для уменьшения накипеобразования широко применяется ее очистка ионнообменными смолами. Ингибиторы коррозии разделяют, в зависимости от условий их применения, на жидкофазные и парофазные или летучие. Жидкофазные ингибиторы делят в свою очередь на ингибиторы коррозии в нейтральных, щелочных и кислых средах. В качестве ингибиторов для нейтральных растворов чаще всего применяются неорганические вещества анионного типа. Их тормозящее действие связано, по-видимому, или с окислением поверхности металла (нитриты, хроматы), или с образованием пленки труднорастворимого соединения между металлом, данным анионом и, возможно, кислородом (фосфаты, гидрофосфаты). Исключение представляют в этом отношении соли бензойной кислоты, ингибирующий эффект которых связан, главным образом, с адсорбционными явлениями. Все ингибиторы для нейтральных сред тормозят преимущественно анодную реакцию, смещая стационарный потенциал в положительную сторону. До настоящего времени еще не удалось найти эффективных ингибиторов коррозии металлов в щелочных растворах. Некоторым тормозящим действием обладают лишь высокомолекулярные соединения. В качестве ингибиторов кислотной коррозии применяются почти исключительно органические вещества, содержащие азот, серу или кислород в виде амино-, имино-, тиогрупп, а также в виде карбоксильных, карбонильных и некоторых других групп. Согласно наиболее распространенному мнению, действие ингибиторов кислотной коррозии связано с их адсорбцией на границе раздела металл - кислота. В результате адсорбции ингибиторов наблюдается торможение катодного и анодного процессов, снижающие скорость коррозии. Действие большинства ингибиторов кислотной коррозии усиливается при одновременном введении добавок поверхностно - активных анионов: галогенидов, сульфидов и роданидов. Парофазные ингибиторы применяются для защиты машин, аппаратов и других металлических изделий во время их эксплуатации в воздушной атмосфере, при транспортировке и хранении. Парофазные ингибиторы вводятся в конвейеры, в упаковочные материалы или помещают в непосредственной близости от работающего агрегата. Благодаря достаточно высокой упругости паров, летучие ингибиторы достигают границы раздела металл - воздух и растворяются в пленке влаги, покрывающей металл. Далее они адсорбируются из раствора на поверхности металла. Тормозящие эффекты в этом случае подобны тем, какие наблюдаются при применение жидкофозных ингибиторов. В качестве парофазных ингибиторов используют обычно амины с небольшим молекулярным весом, в которые введены соответствующие группы, например NО 2 или СО 2 . В связи с особенностями использования парофазных ингибиторов к ним предъявляются повышенные требования в отношении их токсичности. Ингибирование - сложный способ защиты, и его успешное применение в различных условиях требует широких познаний.Протекторная защита и электрозащита.
Протекторная защита применяется в тех случаях, когда защищается конструкция (подземный трубопровод, корпус судна), находящаяся в среде электролита (морская вода, подземные, почвенные воды и т. д.). Сущность такой защиты заключается в том, что конструкцию соединяют с протектором - более активным металлом, чем металл защищаемой конструкции. В качестве протектора при защите стальных изделий обычно используют магний, алюминий, цинк и их сплавы. В процессе коррозии протектор служит анодом и разрушается, тем самым предохраняя от разрушения конструкцию. По мере разрушения протекторов их заменяют новыми. На этом принципе основана и электрозащита. Конструкция, находящаяся в среде электролита, также соединяется с другим металлом (обычно куском железа, рельсом и т. п.), но через внешний источник тока. При этом защищаемую конструкцию присоединяют к катоду, а металл - к аноду источника тока. Электроны отнимаются от анода источником тока, анод (защищающий металл) разрушается, а на катоде происходит восстановление окислителя. Электрозащита имеет преимущество перед протекторной защитой! радиус действия первой около 2000 м, второй - около 50 м. Изменение состава среды. Для замедления коррозии металлических изделий в электролит вводят вещества (чаще всего органические), называемые замедлителями коррозии или ингибиторами. Они применяются в тех случаях, когда металл следует защищать от разъедания кислотами. Советские ученые создали ряд ингибиторов (препараты марок ЧМ, ПБ и др.), которые, будучи добавлены к кислоте, в сотни раз замедляют растворение (коррозию) металлов. В последние годы разработаны летучие (или атмосферные) ингибиторы. Ими пропитывают бумагу, которой оберты-вают металлические изделия. Пары ингибиторов адсорбируются на поверхности металла и образуют на ней защит-ную пленку. Ингибиторы широко применяются при химической очистке от на-кипи паровых котлов, снятии окалины с обработанных изделий, а также при хранении и перевозке соляной кислоты в стальной таре. К числу неорганических ингибиторов относятся нитриты, хроматы, фосфаты, силикаты. Механизм действия ингибиторов является предметом исследования многих химиков.Создание сплавов с антикоррозионными свойствами.
Введением в состав стали до 12% хрома получают нержавеющую сталь, устойчивую к коррозии. Добавки никеля, кобальта и меди усиливают антикоррозионные свойства стали, так как повышается склонность сплавов к пассивации. Создание сплавов с антикоррозионными свойствами- одно из важных направлений борьбы с коррозионными потерями.Цели, задачи и методы исследования
Целью данной исследовательской работы является изучение коррозии и реставрации архитектурных ценностей г. Цивильск и Ивановской сельской администрации. Исходя из цели, были поставлены следующие задачи :Проанализировать литературу по данной проблеме.
Изучить способы защиты от коррозии металлических изделий.
Провести исследование по выявлению архитектурных ценностей г. Цивильска и Ивановской сельской администрации.
Предложить способы защиты исследуемым объектам.
- Сбор и анализ теоретической информации. Поиск памятников культуры: памятников, мемориальных досок и пр. Наблюдения с целью определения материала, из которого изготовлена архитектурная ценность и возможных процессов разрушения.
Результаты исследования
Исследования архитектурных ценностей г. Цивильск и ивановской сельской администрации проводилась в период с ноября по декабрь 2005 года. В ходе экскурсии по г. Цивильск были выявлены следующие достопримечательности:- Памятник, посвященный 400-летию г. Цивильск. Памятник павшим воинам в Великой Отечественной войне. Памятник В. И. Ленину. Экспозиция перед Районным военным комиссариатом. Памятник в честь участника ВОВ жителя г. Цивильск А. Рогожкина. Памятник в честь участника ВОВ жителя г. Цивильск Силантьева. Экспозиция перед детским садом №4.
Архитектурная ценность | Внешний вид (материал, форма) | Способы защиты от коррозии |
||
проводимые | наиболее оптимальные |
|||
г. Цивильск | Памятник, посвященный 400-летию г. Цивильск | |||
Памятник В. И. Ленину | Мраморный Ленин с вытянутой рукой, покрытый краской серебристого цвета, установлен на бетонной поставке высотой около 1 метра. Общая высота композиции составляет около 2,5-3 метров. | Регулярное окрашивание памятника включая постамент краской. Однако это не спасает от механических разрушений под воздействием ветра, воды и солнца. Заметна трещина на ноге. | Необходима реставрационная работа по устранению трещины. Желательно использование специальных алкидных красок для нанесения на поверхность памятяника. | |
По своей архитектуре и материалу аналогичен памятнику Ленина. В композицию входят – солдат из мрамора, покрыт серебристой краской, расположен на бетонной подставке высотой 1 метр. Подставка обложена металлическими листами. Общая высота – около 5 метров. Рядом расположена мемориальная доска, представляющая собой длинную кирпичную стену, на которую вмонтированы оцинкованные листы с фамилиями участников ВОВ, не вернувшихся с фронта. | Окрашивание краской проводится, однако из-за большой высоты памятника нерегулярно. Коррозии не подвергается. | Необходима очистка памятника от засохших листьев и веток. | ||
Экспозиция перед Районным военным комиссариатом | Пушка, установленная на подставке из кирпича. Высота около 2 метров. Металлическая (сталь), зеленого цвета. На стволе пушки надпил глубиной 4 см. | Пушка регулярно окрашивается работниками комиссариата алкидной краской зеленого цвета, правда несколько другого оттенка, чем изначальный цвет изделия. Надпил на стволе способствует разрушению. | Возможна протекторная защита, в качестве протектора можно использовать заклепки и пластины из цинка. |
|
Памятник в честь участника ВОВ жителя г. Цивильск А. Рогожкина | На подставке из бетона мраморная плита зеленого цвета. В плиту вмонтирован барельеф из коррозионноустойчивого сплава с изображением моряка Силантьева. | Реставрация памятника не проводилась очень давно. Заметны трещины на мраморной плите. Барельеф не корродирует, однако заметны отколотые части. | Уход и своевременная замена мраморной плиты, наиболее сильно подверженной разрушениям. |
|
Памятник в честь участника ВОВ жителя г. Цивильск Силантьева | Аналогичен памятнику в честь Рогожкина. Барельеф из устойчивого сплава с изображением Силантьева закреплен на мраморной подставке в виде треугольника. | Барельеф не подвергается коррозии. | Своевременное покрытие защитными составами несущих конструкций. | |
Экспозиция перед детским садом №4. | Статуи двух пионеров с горнами. | |||
п. Опытный | Памятник павшим воинам в Великой Отечественной войне | На стене из белого кирпича расположен барельеф с изображением воюющих солдат, выкрашенный золотистой краской. | Коррозии не подвергается. Окрашивается регулярно. Заметны трещины на барельефе. | Устранение трещины. |
с. Иваново | Мемориальная доска павшим воинам в Великой Отечественной войне | |||
д. Синья-Котяки | Памятник в честь 60-летия Победы в Великой Отечественной войне (воздвигнут в июле 2004 года). | Памятник изготовлен из мраморной крошки, обложенной белым кирпичом. Надписи на мемориале выкрашены в золотисты цвет. | Коррозии практически не подвергается. Может разрушаться кирпич под действием ветра, солнца и воды. | Регулярнее подкрашивание букв, своевременная замена несущих конструкций. |
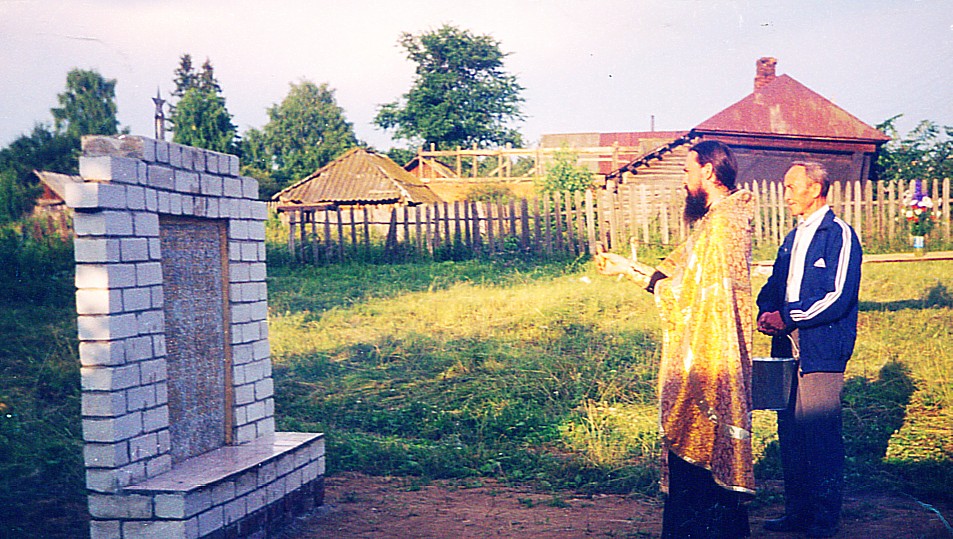
Выводы
В результате исследования архитектурных ценностей г. Цивильск и Ивановской сельской администрации мы получили важную информацию о состоянии памятников и способах их сохранения.Самопроизвольное окисление металлов, вредное для промышленной практики (уменьшающее долговечность изделий), называется коррозией. Среда, в которой металл подвергается коррозии (корродирует), называется коррозионной, или агрессивной.
Способов защиты металлов от коррозии много. Наиболее эффективными среди них являются протектирование, ингибирование, создание защитного слоя (лаки, краски, эмали) и антикоррозионный сплавов.
В г. Цивильск выявлено шесть главных достопримечательностей. Каждый исследуемый населенный пункт Ивановской сельской администрации содержит по одной архитектурной ценности, посвященной Великой Отечественной войне. В целом эти памятники представляют собой сложные композиции, изготовленные из мрамора, с добавлением металлических фрагментов. Коррозии подвергается лишь пушка перед Районным военным комиссариатом.
Для защиты от коррозии исследуемым объектам рекомендован своевременный уход и очистка, некоторым (памятник Ленину, памятник в честь павших воинов г. Цивильск) – регулярная окраска специальными составами. Памятнику в честь моряка Рогожкина требуется реставрация несущей конструкции. Для пушки, наиболее подверженной коррозии, мы предлагаем также протекторную защиту.
Список использованной литературы
- Ахметов Н.С., Общая и неорганическая химия. - М.: Высшая школа, 1989 Некрасов Б.В., Учебник общей химии. - М.: Химия, 1981 Коттон Ф., Уилкинсон Дж., Основы неорганической химии. - М.: Мир, 1979 Карапетьянц М.Х., Дракин С.И., Общая и неорганическая химия. - М.: Химия, 1993 Яковлев А. А. В мире камня. М.: Детгиз, 1991
1 От латинского соrrоdеге-разъедать.