Uno de los factores más comunes y al mismo tiempo destructivos que afectan a un automóvil durante su funcionamiento es la corrosión. Se han desarrollado varios métodos para proteger la carrocería de él, y existen tanto medidas dirigidas específicamente contra este fenómeno, como tecnologías complejas para proteger el automóvil, protegiéndolo de diversos factores. Este artículo analiza la protección electroquímica del cuerpo.
Causas de la corrosión
Dado que el método electroquímico de protección de un automóvil está dirigido exclusivamente contra la corrosión, se deben considerar las razones que causan daños a la carrocería. Los principales son el agua y los reactivos para carreteras utilizados durante la estación fría. Cuando se combinan entre sí, forman una solución salina altamente concentrada. Además, la suciedad depositada en el cuerpo retiene la humedad en los poros durante mucho tiempo y, si contiene reactivos para la carretera, también atrae moléculas de agua del aire.
La situación se agrava si la pintura del coche presenta defectos, aunque sean pequeños. En este caso, la propagación de la corrosión se producirá muy rápidamente e incluso las capas protectoras restantes en forma de imprimación y galvanización pueden no detener este proceso. Por lo tanto, es importante no sólo limpiar constantemente el automóvil de la suciedad, sino también controlar el estado de la pintura. Las fluctuaciones de temperatura y las vibraciones también influyen en la propagación de la corrosión.
También debes tener en cuenta las zonas del coche que son más susceptibles a la corrosión. Éstas incluyen:
- partes ubicadas más cercanas a la superficie de la carretera, es decir, umbrales, guardabarros y bajos;
- soldaduras restantes después de las reparaciones, especialmente si se realizaron incorrectamente. Esto se explica por el "debilitamiento" del metal a altas temperaturas;
- Además, el óxido suele afectar a diversas cavidades ocultas y mal ventiladas donde se acumula la humedad y no se seca durante mucho tiempo.
Principio de funcionamiento de la protección electroquímica.
El método considerado para proteger la carrocería del óxido se clasifica como métodos activos. La diferencia entre ellos y los métodos pasivos es que los primeros crean algún tipo de medidas de protección que no permiten que los factores que causan corrosión afecten al automóvil, mientras que los segundos solo aíslan la carrocería de la exposición al aire atmosférico. Esta tecnología se utilizó originalmente para proteger tuberías y estructuras metálicas de la oxidación. El método electroquímico se considera uno de los más eficaces.
Este método de protección corporal, también llamado catódico, se basa en las peculiaridades de las reacciones redox. La esencia es que se aplica una carga negativa a la superficie protegida.
El cambio de potencial se lleva a cabo utilizando una fuente externa de corriente continua o conectándolo a un ánodo de sacrificio que consiste en un metal que es más electronegativo que el objeto a proteger.
El principio de funcionamiento de la protección electroquímica de un automóvil es que entre la superficie de la carrocería y la superficie de los objetos circundantes, debido a la diferencia de potencial entre ellos, pasa una corriente débil a través de un circuito representado por aire húmedo. En tales condiciones, el metal más activo se oxida y el otro, por el contrario, se reduce. Por este motivo, las placas protectoras de metales electronegativos que se utilizan en los automóviles se denominan ánodos de sacrificio. Sin embargo, si el potencial se desplaza excesivamente en la dirección negativa, es posible que se produzca desprendimiento de hidrógeno, un cambio en la composición de la capa cercana al electrodo y otros fenómenos que conducen a la degradación de la capa protectora y a la aparición de corrosión bajo tensión de la superficie protegida. objeto.
La tecnología que se está considerando para los automóviles implica el uso de la carrocería como cátodo (polo con carga negativa), y varios objetos o elementos circundantes instalados en el automóvil que conducen la corriente, por ejemplo, estructuras metálicas o superficies de carreteras mojadas, sirven como ánodos (polos con carga positiva). ). En este caso, el ánodo debe estar compuesto de un metal activo, como magnesio, zinc, cromo o aluminio.
Muchas fuentes dan la diferencia de potencial entre el cátodo y el ánodo. Según ellos, para crear una protección completa contra la corrosión del hierro y sus aleaciones, es necesario alcanzar un potencial de 0,1-0,2 V. Valores grandes tienen poco efecto sobre el grado de protección. En este caso, la densidad de corriente protectora debería ser de 10 a 30 mA/m².
Sin embargo, estos datos no son del todo correctos: de acuerdo con las leyes de la electroquímica, la distancia entre el cátodo y el ánodo es directamente proporcional a la magnitud de la diferencia de potencial. Por tanto, en cada caso concreto es necesario alcanzar un determinado valor de diferencia de potencial. Además, el aire, considerado como electrolito en este proceso, es capaz de conducir corriente eléctrica caracterizada por una gran diferencia de potencial (aproximadamente kW), por lo que una corriente con una densidad de 10-30 mA/m² no será conducida por el aire. Sólo puede producirse una corriente "lateral" como resultado de que el ánodo se moje.
En cuanto a la diferencia de potencial, se observa polarización de la concentración respecto al oxígeno. En este caso, las moléculas de agua que caen sobre la superficie de los electrodos se orientan hacia ellos de tal forma que se liberan electrones, es decir, se produce una reacción de oxidación. En el cátodo, esta reacción, por el contrario, se detiene. Debido a la ausencia corriente eléctrica La liberación de electrones se produce lentamente, por lo que el proceso es seguro e invisible. Debido al efecto de polarización, se produce un desplazamiento adicional del potencial de la carrocería en dirección negativa, lo que permite desconectar periódicamente el dispositivo de protección contra la corrosión. Cabe señalar que el área del ánodo es directamente proporcional a la eficacia de la protección electroquímica.
Opciones de creación
En cualquier caso, el papel del cátodo lo desempeñará la carrocería del automóvil. El usuario debe seleccionar un elemento que se utilizará como ánodo. La elección se realiza en función de las condiciones de funcionamiento del vehículo:
- Para automóviles parados, un objeto metálico ubicado cerca, por ejemplo, un garaje (siempre que esté construido de metal o tenga elementos metálicos), o un circuito de tierra, que se puede instalar en ausencia de un garaje en un estacionamiento abierto. mucho, puede servir como cátodo.
- En un vehículo en movimiento, se pueden utilizar dispositivos como una “cola” de conexión a tierra de caucho metalizado y protectores (electrodos protectores) montados en la carrocería.
Debido a la ausencia de corriente que fluye entre los electrodos, basta con conectar la red de +12 voltios a bordo del automóvil a uno o más ánodos a través de una resistencia adicional. último dispositivo Sirve para limitar la corriente de descarga de la batería en caso de un cortocircuito entre ánodo y cátodo. Las principales causas de los cortocircuitos son la instalación inadecuada de los equipos, daños al ánodo o su descomposición química por oxidación. A continuación, analizamos las características del uso de los elementos enumerados anteriormente como ánodos.
Usar un garaje como ánodo se considera lo más de una manera sencilla Protección electroquímica de la carrocería de un automóvil parado. Si la habitación tiene un piso de metal o un revestimiento de piso con áreas expuestas de refuerzo de hierro, también se proporcionará protección inferior. Durante los períodos cálidos, se observa un efecto invernadero en los garajes metálicos, pero si se crea una protección electroquímica, esta no destruye el automóvil, sino que tiene como objetivo proteger su carrocería de la corrosión.
Crear protección electroquímica en presencia de un garaje metálico es muy sencillo. Para hacer esto, simplemente conecte este objeto al conector positivo. batería automóvil a través de una resistencia adicional y un cable de montaje.
Incluso el encendedor de cigarrillos se puede utilizar como conector positivo, siempre que haya voltaje en él cuando se apaga el interruptor de encendido (no todos los automóviles tienen este dispositivo que permanece operativo cuando se apaga el motor).
Al crear protección electroquímica, el circuito de tierra se utiliza como ánodo de acuerdo con el mismo principio que el garaje metálico discutido anteriormente. La diferencia es que el garaje protege toda la carrocería del coche, mientras que este método sólo protege la parte inferior. Se crea un circuito de conexión a tierra introduciendo cuatro varillas de metal de al menos 1 m de largo en el suelo alrededor del perímetro del automóvil y estirando un cable entre ellas. El circuito está conectado al coche, así como al garaje, a través de una resistencia adicional.
Una “cola” de conexión a tierra metalizada de caucho es la forma más sencilla de proteger electroquímicamente un vehículo en movimiento contra la corrosión. Este dispositivo es una tira de goma con elementos metálicos. El principio de su funcionamiento es que en condiciones de alta humedad, surge una diferencia de potencial entre la carrocería del automóvil y la superficie de la carretera. Además, cuanto mayor sea la humedad, mayor será la eficacia de la protección electroquímica creada por el elemento en cuestión. La “cola” de conexión a tierra está instalada en la parte trasera del automóvil de tal manera que está expuesta a salpicaduras de agua que salen de debajo de la rueda trasera cuando se conduce sobre una superficie de carretera mojada, ya que esto aumenta la eficiencia de la protección electroquímica.
La ventaja de la cola de conexión a tierra es que, además de la función de protección electroquímica, alivia la carrocería del automóvil de la tensión estática. Esto es especialmente cierto para los vehículos que transportan combustible, ya que una chispa electrostática, que es el resultado de la acumulación de carga estática durante el movimiento, es peligrosa para la carga que transporta. Por lo tanto, los dispositivos en forma de cadenas metálicas que se arrastran por la superficie de la carretera se encuentran, por ejemplo, en los camiones de combustible.
En cualquier caso, es necesario aislar la cola de tierra de la carrocería del automóvil mediante corriente continua y, a la inversa, “cortocircuitarla” mediante corriente alterna. Esto se logra mediante el uso de un circuito RC, que es un filtro de frecuencia básico.
La protección de un automóvil contra la corrosión mediante un método electroquímico utilizando electrodos protectores como ánodos también está diseñada para funcionar en movimiento. Los protectores se instalan en las zonas más vulnerables de la carrocería a la corrosión, representadas por los umbrales, guardabarros y bajos.
Los electrodos protectores, como en todos los casos discutidos anteriormente, funcionan según el principio de crear una diferencia de potencial. La ventaja del método considerado es la presencia constante de ánodos, independientemente de si el vehículo está parado o en movimiento. Por tanto, esta tecnología se considera muy eficaz, pero es la más difícil de crear. Esto se debe al hecho de que para garantizar una alta eficacia de protección, es necesario instalar entre 15 y 20 protectores en la carrocería del automóvil.
Como electrodos protectores se pueden utilizar elementos fabricados con materiales como aluminio, acero inoxidable, magnetita, platino, carboxilo y grafito. Las dos primeras opciones se clasifican como destructibles, es decir, los electrodos protectores que las componen deben cambiarse a intervalos de 4 a 5 años, mientras que el resto se denominan no destructibles, ya que se caracterizan por una durabilidad significativamente mayor. En cualquier caso, los protectores son placas redondas o rectangulares con una superficie de 4-10 cm².
En el proceso de creación de dicha protección, es necesario tener en cuenta algunas características de los protectores:
- el radio de acción protectora se extiende a 0,25-0,35 m;
- los electrodos deben instalarse únicamente en áreas que tengan una capa de pintura;
- para fijar los elementos en cuestión se debe utilizar pegamento o masilla epoxi;
- Se recomienda limpiar el brillo antes de la instalación;
- el lado exterior de los protectores no debe recubrirse con pintura, masilla, pegamento u otras sustancias aislantes eléctricas;
- Dado que los electrodos protectores son placas de condensadores cargadas positivamente, deben estar aislados de la superficie cargada negativamente de la carrocería del automóvil.
El papel de junta dieléctrica del condensador lo desempeñará la capa de pintura y el pegamento ubicado entre los protectores y la carrocería del automóvil. También se debe tener en cuenta que la distancia entre los protectores es directamente proporcional a la campo eléctrico, por lo que deben instalarse a una pequeña distancia entre sí para garantizar una capacidad suficiente del condensador.
Los cables se alimentan a los electrodos protectores a través de perforaciones en los tapones de goma que cubren los orificios en la parte inferior del automóvil. Puedes instalar muchos protectores pequeños o menos electrodos protectores en tu coche tamaño más grande. En cualquier caso, es necesario utilizar estos elementos en las zonas más vulnerables a la corrosión, mirando hacia el exterior, ya que la función del electrolito en este caso la realiza el aire.
Después de instalar una protección electroquímica de este tipo, la carrocería del automóvil no recibirá una descarga eléctrica, ya que genera muy poca electricidad. Incluso si una persona toca el electrodo protector, no recibirá una descarga. Esto se explica por el hecho de que la protección electroquímica anticorrosión utiliza corriente continua de baja potencia, lo que crea un campo eléctrico débil. Además, existe una teoría alternativa según la cual el campo magnético existe sólo entre la superficie del cuerpo y el lugar de instalación de los electrodos protectores. Por tanto, el campo electromagnético creado por la protección electroquímica es más de 100 veces más débil que el campo electromagnético de un teléfono móvil.
La protección de sacrificio es un tipo de protección catódica. Se adjunta un metal más electronegativo, un protector, a la estructura protegida que, al disolverse en el medio ambiente, protege la estructura principal de la destrucción. Después de la completa disolución del protector o pérdida de contacto con la estructura protegida, se debe reemplazar el protector.
El protector funciona eficazmente si la resistencia de transición entre él y ambiente poco. La acción de la banda de rodadura está limitada a una determinada distancia. La distancia máxima posible desde la estructura que se está protegiendo se denomina radio de protección del protector.
La protección de sacrificio se utiliza en los casos en que la obtención de energía externa para organizar la protección catódica se asocia con dificultades y la construcción de líneas eléctricas especiales no es económicamente rentable.
La protección protectora se utiliza para combatir la corrosión de estructuras metálicas en agua de mar y río, suelo y otros ambientes neutros. El uso de protectores en soluciones ácidas no es práctico debido a la alta tasa de autodisolución.
Sin embargo, no siempre es aconsejable utilizar metal puro como protectores. Por ejemplo, el zinc puro se disuelve de manera desigual debido a su estructura dendrítica de grano grueso, la superficie del aluminio puro está cubierta con una densa película de óxido, el magnesio tiene una alta tasa de corrosión propia. Para dar a los protectores las propiedades operativas requeridas, se introducen elementos de aleación en su composición.
(de centésimas a décimas de porcentaje), contribuyendo al cambio requerido en los parámetros de la red. Las aleaciones de magnesio para bandas de rodadura contienen A1 (5-7%) y Zn (2-5%) como aditivos de aleación; contenido de impurezas como
Mantener al nivel de décimas o centésimas de porcentaje. El hierro como material de la banda de rodadura se utiliza en su forma pura (Re-armco) o en forma de acero al carbono.
u óxido de zinc 2nO.
Los protectores de aluminio se utilizan para proteger estructuras que operan en agua de mar corriente, así como para proteger instalaciones portuarias y estructuras ubicadas en la plataforma costera.
Los protectores de magnesio se utilizan principalmente para proteger estructuras pequeñas en entornos débilmente conductores de electricidad donde la eficacia de los protectores de aluminio y zinc es baja: suelos, aguas dulces o ligeramente saladas. Sin embargo, debido a la alta tasa de autodisolución y la tendencia a formar compuestos poco solubles en la superficie, el área de acción de los protectores de magnesio se limita a ambientes con pH = 9,5-10,5. Al proteger sistemas cerrados, como tanques, con protectores de magnesio, es necesario tener en cuenta la posibilidad de formación de gas detonante debido a la liberación de hidrógeno en la reacción catódica que ocurre en la superficie de la aleación de magnesio. El uso de protectores de magnesio también está asociado con el riesgo de fragilización por hidrógeno y agrietamiento por corrosión de los equipos.
Cualquier producto metálico se destruye fácilmente bajo la influencia de ciertos factores externos, con mayor frecuencia la humedad. Para prevenir tales fenómenos, se utiliza protección protectora contra la corrosión. Su tarea es reducir el potencial del material base y así protegerlo de la corrosión.
La esencia del procedimiento.
La protección protectora se basa en una sustancia llamada inhibidor. Este es un metal con mayores propiedades electronegativas. Cuando se expone al aire, el protector se disuelve. Como resultado, el material base se conserva incluso si se ve gravemente afectado por la corrosión.
Se pueden vencer fácilmente varios tipos de corrosión si se utilizan métodos electroquímicos catódicos, que incluyen protección de sacrificio. Este procedimiento es una solución ideal cuando una empresa no tiene la capacidad financiera o el potencial tecnológico para brindar una protección completa contra los procesos de corrosión.
Ventajas principales
La protección protectora de los metales contra la corrosión es Buen camino protección de cualquier superficie metálica. Su uso es aconsejable en varios casos:
- Cuando una empresa no tiene suficiente capacidad de producción para utilizar técnicas más intensivas en energía.
- Cuando necesitas proteger pequeñas estructuras.
- Si se requiere protección de productos y objetos metálicos cuyas superficies estén recubiertas con materiales aislantes.
Para lograr la máxima eficiencia, es aconsejable utilizar protección de la banda de rodadura en un entorno electrolítico.
¿Cuándo se requiere protección?
La corrosión ocurre en cualquier superficie metálica en una amplia variedad de áreas, desde la industria del petróleo y el gas hasta la construcción naval. La protección contra la corrosión se utiliza ampliamente al pintar cascos de camiones cisterna. Estos recipientes están constantemente expuestos al agua y una pintura especial no siempre evita las reacciones de humedad con la superficie del metal. El uso de protectores es una solución sencilla y eficaz al problema, especialmente si los vasos van a estar en funcionamiento durante mucho tiempo.
La mayoría de las estructuras metálicas están creadas a partir de acero, por lo que es recomendable utilizar protectores que tengan un potencial de electrodo negativo. Tres metales son básicos para la producción de protectores: zinc, magnesio y aluminio. Debido a la gran diferencia de potencial entre estos metales y el acero, el radio de acción protectora se amplía y cualquier tipo de corrosión se elimina fácilmente.
¿Qué metales se utilizan?
El sistema de protección está construido a base de diversas aleaciones, dependiendo del uso específico de los protectores, por ejemplo, del entorno en el que se utilizará. La protección protectora contra la corrosión suele ser necesaria para los productos de hierro y acero, pero también las superficies de zinc, aluminio, cadmio o magnesio. Una característica especial de la protección sacrificial es el uso de ánodos galvánicos, que protegen las tuberías de la corrosión del suelo. El cálculo de dichas instalaciones se realiza teniendo en cuenta una serie de parámetros:
- fuerza actual en el protector;
- indicadores de su resistencia;
- grado de protección requerido para 1 km de tubería;
- número de huellas para el mismo segmento;
- la distancia que existe entre los elementos del sistema de protección.
Pros y contras de diferentes protectores.
La protección se construye a base de protectores. estructuras de construccion de corrosión, tuberías diferentes tipos(distribución, principal, campo). Sin embargo, es necesario utilizarlos con prudencia:
- es aconsejable el uso de protectores de aluminio con el fin de proteger estructuras y estructuras en el agua de mar y la plataforma costera;
- Los de magnesio son adecuados para su uso en entornos débilmente conductores de electricidad donde los protectores de aluminio y zinc muestran una baja eficiencia. Pero no se pueden utilizar si es necesario para proteger las superficies internas de camiones cisterna, tanques y tanques de sedimentación de petróleo, ya que los protectores de magnesio se caracterizan por un mayor riesgo de explosión e incendio. Idealmente, los proyectores basados en este elemento deberían usarse para la protección externa de estructuras que se utilizan en un ambiente fresco;
- Los protectores de zinc son completamente seguros, por lo que se pueden utilizar en cualquier objeto, incluso si tienen un alto nivel de riesgo de incendio.
Si el revestimiento es pintura.
Muy a menudo es necesario proteger un oleoducto o gasoducto de la corrosión, teniendo en cuenta la capa de pintura. Combinarlo con un protector es una forma pasiva de proteger las estructuras de la corrosión. Al mismo tiempo, la efectividad de tal evento no es tan alta, pero se logra lo siguiente:
- se nivelan los defectos en los revestimientos de estructuras metálicas y tuberías, por ejemplo, descamaciones, grietas;
- se reduce el consumo de materiales protectores, mientras que la protección en sí es más duradera;
- la corriente protectora se distribuye uniformemente sobre la superficie metálica del producto u objeto.
La protección protectora contra la corrosión en combinación con pinturas y barnices es la capacidad de distribuir la corriente protectora precisamente a aquellas superficies que requieren la máxima atención.
Acerca de la protección de tuberías
Como lo usas tubos metálicos están expuestos a la corrosión por dentro y por fuera. La placa aparece debido a que por las tuberías fluyen sustancias agresivas que reaccionan con los materiales. El estado interno de los productos metálicos se ve afectado por los altos niveles de humedad del suelo. Si no se piensa en una protección de alta calidad de las estructuras de los edificios contra la corrosión, sucederá lo siguiente:
- la tubería comenzará a colapsar desde el interior;
- será necesario realizar inspecciones preventivas de las carreteras con mayor frecuencia;
- se requerirán reparaciones más frecuentes, lo que generará costos adicionales;
- será necesario detener total o parcialmente una refinería de petróleo u otro complejo industrial.
Hay varias formas de proteger las tuberías: pasiva y activa. Reducir la agresividad del medio ambiente también puede servir como medio de protección. Para garantizar una protección integral, se tienen en cuenta el tipo de tubería, el método de instalación y la interacción con el medio ambiente.
Métodos de protección pasivos y activos.
Todos los métodos principales para proteger las tuberías de la corrosión se reducen a realizar una serie de trabajos. Si hablamos de métodos pasivos, se expresan de la siguiente manera:
- un método de instalación especial, cuando la resistencia a la corrosión se piensa en la etapa de instalación de la tubería. Para ello, se deja un espacio de aire entre el suelo y la tubería, gracias al cual nada entrará en la tubería. agua subterránea, sin sal, sin álcali;
- aplicar recubrimientos especiales a las tuberías que protegerán la superficie de las influencias del suelo;
- tratamiento con productos químicos especiales, por ejemplo, fosfatos, que forman una película protectora en la superficie.
Esquema de protección basado métodos activos Implica el uso de corriente eléctrica y reacciones electroquímicas de intercambio iónico:
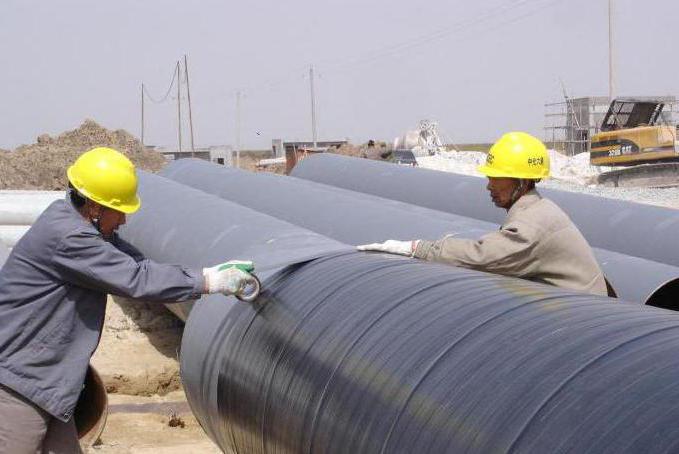
El caso de la protección de la banda de rodadura
Como puede ver, existen muchas formas de mejorar las características protectoras de tuberías y otros productos metálicos. Pero todos ellos requieren el gasto de corriente eléctrica. La protección protectora contra la corrosión de las tuberías es una solución más ventajosa, ya que todos los procesos de oxidación se detienen simplemente aplicando aleaciones de otros materiales a la superficie de las tuberías metálicas. Los siguientes factores hablan a favor de este método:
- rentabilidad y simplicidad del proceso debido a la ausencia de una fuente de corriente continua y el uso de aleaciones de magnesio, zinc o aluminio;
- la posibilidad de utilizar instalaciones individuales o grupales, mientras que el esquema de protección de la banda de rodadura se piensa teniendo en cuenta las características de la instalación diseñada o ya construida;
- Posibilidad de uso en cualquier suelo y en condiciones de mar/océano donde es costoso o imposible utilizar fuentes de corriente externas.
La protección de la banda de rodadura se puede utilizar para aumentar la resistencia a la corrosión de varios tanques, cascos de barcos y tanques que se utilizan en condiciones extremas.
3.1 Protección catódica
Protección catódica - el tipo más común de protección electroquímica. Se utiliza en los casos en que el metal no es propenso a la pasivación, es decir, tiene una región extendida de disolución activa, una región pasiva estrecha, valores altos de corriente de pasivación (i p) y potencial de pasivación (φ p).
La polarización catódica se puede lograr conectando la estructura a proteger al polo negativo de una fuente de corriente externa o a un metal que tenga un potencial de electrodo más electronegativo. En este último caso, no es necesaria una fuente de corriente externa, ya que con el mismo sentido de la corriente se forma un elemento galvánico, es decir, la parte protegida se convierte en cátodo, y el metal más electronegativo, llamado protector, - ánodo.
Protección catódica corriente externa. La protección catódica mediante polarización de una fuente de corriente externa se utiliza para proteger equipos fabricados con aceros al carbono, de baja y alta aleación y con alto contenido de cromo, estaño, zinc, cobre y aleaciones de cobre-níquel, aluminio y sus aleaciones, plomo, titanio y sus aleaciones. Por regla general, se trata de estructuras subterráneas (tuberías y cables para diversos fines, cimientos, equipos de perforación), equipos operados en contacto con agua de mar(cascos de barcos, partes metálicas de estructuras costeras, plataformas de perforación marinas), superficies internas de aparatos y tanques de la industria química. A menudo, la protección catódica se utiliza simultáneamente con la aplicación de revestimientos protectores. Una disminución en la velocidad de autodisolución de un metal durante su polarización externa se denomina efecto protector. El criterio principal para la protección catódica es el potencial protector. El potencial protector es el potencial al cual la velocidad de disolución del metal adquiere un valor extremadamente bajo aceptable para las condiciones de operación dadas. La característica de la protección catódica es el valor del efecto protector Z,%:Donde K 0 [g/(m 2 h)] es la velocidad de corrosión del metal sin protección, K 1 [g/(m 2 h)] es la velocidad de corrosión del metal en condiciones de protección electroquímica. El coeficiente de acción protectora K 3 [g/A] está determinado por la fórmula
K 3 = (metro 0 - metro yo)/yo K,
Donde m o y m i son la pérdida de masa del metal, respectivamente, sin protección catódica y con su uso, g/m 2 ; i a [A/m 2 ] - densidad de corriente del cátodo. El diagrama de protección catódica se muestra en la Fig. 51. El polo negativo de la fuente de corriente externa 4 está conectado a la estructura metálica protegida 1, y el polo positivo está conectado al electrodo auxiliar 2, que funciona como ánodo. Durante el proceso de protección, el ánodo se destruye activamente y está sujeto a restauración periódica.
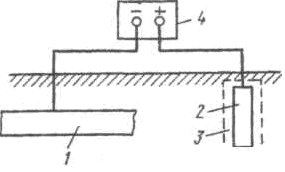
Figura 53 - Esquema de protección de sacrificio de tubería El protector funciona eficazmente si la resistencia de transición entre él y el medio ambiente es baja. Durante el funcionamiento, un protector, por ejemplo el zinc, puede cubrirse con una capa de productos de corrosión insolubles, que lo aíslan del medio ambiente y aumentan considerablemente la resistencia de contacto. Para combatir esto, el protector se coloca en un relleno. 4
- una mezcla de sales que crea un determinado ambiente a su alrededor, facilitando la disolución de los productos de corrosión y aumentando la eficacia y estabilidad de la banda de rodadura en el suelo 1. La acción de la banda de rodadura se limita a una determinada distancia. La distancia máxima posible del protector a la estructura protegida se denomina radio de acción del protector. Depende de una serie de factores, los más importantes de los cuales son la conductividad eléctrica del medio, la diferencia de potencial entre el protector y la estructura protegida y las características de polarización. A medida que aumenta la conductividad eléctrica del medio, el efecto protector del protector se extiende a una distancia mayor. Así, el radio de acción de un protector de zinc al proteger acero en agua destilada es de 0,1 cm, en agua de mar de 4 m, en una solución de NaCl al 3%. 6
m) En comparación con la protección catódica por corriente externa, es aconsejable utilizar protección de sacrificio en los casos en que la obtención de energía del exterior esté asociada a dificultades o si la construcción de líneas eléctricas especiales no sea económicamente rentable. Actualmente, la protección de la banda de rodadura se utiliza para combatir la corrosión de estructuras metálicas.
en agua de mar y río, suelo y otros neutros.
entornos Uso de protección de la banda de rodadura en ambientes ácidos.
entornos está limitado por la alta tasa de autodisolución del protector. Como protectores se pueden utilizar metales: Al, Fe, Mg, Zn. Sin embargo, no siempre es aconsejable utilizar metales puros como protectores. Por ejemplo, el zinc puro se disuelve de manera desigual debido a su estructura dendrítica de grano grueso, la superficie del aluminio puro está cubierta con una densa película de óxido, el magnesio tiene una alta tasa de corrosión propia. Para dar a los protectores las propiedades operativas requeridas, se introducen elementos de aleación en su composición. En la composición de los protectores de zinc se introducen Cd (0,025-0,15%) y A1 (0,1-0,5%). Intentan mantener el contenido de impurezas como Fe, Cu, Pb en un nivel no superior al 0,001-0,005%. Se introducen aditivos en la composición de los protectores de aluminio que evitan la formación de capas de óxido en su superficie: Zn (hasta un 8%), Mg (hasta un 5%), así como Cd, In, Gl, Hg, Tl, Mn. , Si (de centésimas a décimas de porcentaje), contribuyendo al cambio requerido en los parámetros de la red. Las aleaciones de magnesio para bandas de rodadura contienen Al como aditivo de aleación.
(5-7%) y Zn (2-5%); el contenido de impurezas como Fe, Ni, Cu, Pb, Si se mantiene en décimas o centésimas de porcentaje. El hierro como material de la banda de rodadura se utiliza en su forma pura (Fe-armco) o en forma de acero al carbono. Los protectores de zinc se utilizan para proteger equipos que operan en agua de mar (embarcaciones, tuberías, estructuras costeras). Su uso en suelos y aguas dulces ligeramente saladas está limitado debido a la formación de capas de hidróxido de Zn(OH)2 u óxido de zinc ZnO en su superficie. Los protectores de aluminio se utilizan para proteger estructuras que operan en agua de mar corriente, así como para proteger instalaciones portuarias y estructuras ubicadas en la plataforma costera. Los protectores de magnesio se utilizan principalmente para proteger estructuras pequeñas en entornos débilmente conductores de electricidad donde la eficacia de los protectores de aluminio y zinc es baja: suelos, aguas dulces o ligeramente saladas. Sin embargo, debido a la alta tasa de autodisolución y la tendencia a formar compuestos poco solubles en la superficie, el campo de acción de los protectores de magnesio se limita a ambientes con pH = 9,5 – 10,5. Al proteger sistemas cerrados, como tanques, con protectores de magnesio, es necesario tener en cuenta la posibilidad de formación de gas detonante debido a la liberación de hidrógeno en la reacción catódica que ocurre en la superficie de la aleación de magnesio. El uso de protectores de magnesio también está asociado con el riesgo de fragilización por hidrógeno y agrietamiento por corrosión de los equipos. Como en el caso de la protección catódica con corriente externa, la eficacia de la protección sacrificial aumenta cuando se utiliza en combinación con revestimientos protectores. Por lo tanto, la aplicación de un recubrimiento bituminoso a las tuberías mejora significativamente la distribución de la corriente protectora, reduce la cantidad de ánodos y aumenta la longitud de la sección de la tubería protegida con un protector. Si un ánodo de magnesio puede proteger una tubería no revestida con una longitud de sólo 30 m, entonces la protección de una tubería recubierta de betún es eficaz en una longitud de hasta 8 km.
3.2 Protección anódica
Protección anódica se utiliza cuando se operan equipos en entornos altamente conductores de electricidad y están hechos de materiales fácilmente pasivados: carbono, aceros inoxidables de baja aleación, titanio, aleaciones a base de hierro de alta aleación. La protección anódica es prometedora en el caso de equipos fabricados con diferentes materiales pasivantes, por ejemplo, aceros inoxidables de diversas composiciones y uniones soldadas. La protección anódica se realiza conectando la estructura metálica protegida al polo positivo de una fuente externa de corriente continua o a un metal con un potencial más positivo (protector catódico), en este caso el potencial del metal protegido se desplaza en la dirección positiva. hasta alcanzar un estado pasivo estable (Fig. 50). Como resultado, no sólo se produce una reducción significativa (miles de veces) en la tasa de corrosión del metal, sino también se evita que los productos de su disolución entren en el producto fabricado. Los cátodos utilizados para la protección anódica de una fuente de corriente externa deben tener una alta estabilidad en un ambiente corrosivo. La elección del material del cátodo está determinada por las características del medio. Se utilizan materiales como Pt, Ta, Pb, Ni, latón platinado, aceros inoxidables de alta aleación, etc.. La disposición de los cátodos está diseñada individualmente para cada carcasa de protección específica. Como proyector catódico se pueden utilizar materiales como carbono, dióxido de manganeso, magnetita y dióxido de plomo, que tienen un potencial muy positivo. La protección anódica de una fuente externa se basa en hacer pasar corriente a través del objeto protegido y cambiar el potencial de corrosión hacia valores más positivos. La instalación para protección anódica consta de un objeto de protección, un cátodo, un electrodo de referencia y una fuente de corriente eléctrica. La condición principal para la posibilidad de utilizar protección anódica es la presencia de una región extendida de pasividad estable del metal a una densidad de corriente de disolución del metal de no más de (1,5-6,0)·10 -1 A/m 2. El criterio principal que caracteriza el estado de la superficie del metal es el potencial del electrodo. Normalmente, la posibilidad de utilizar protección anódica para un metal o aleación particular se determina tomando curvas de polarización anódica. En este caso se obtienen los siguientes datos: a) el potencial de corrosión del metal en la solución de prueba; b) la extensión del área de pasividad estable; c) densidad de corriente en la región de pasividad estable. La eficacia de la protección se define como la relación entre la velocidad de corrosión sin protección y la velocidad de corrosión bajo protección. Como regla general, los parámetros de protección anódica obtenidos en condiciones de laboratorio y de producción concuerdan entre sí. Dependiendo de las condiciones de funcionamiento específicas, el área de potenciales de protección durante la protección anódica es 0,3-1,5 V más positiva que el potencial de corrosión libre y la velocidad de disolución de los metales puede disminuir miles de veces. Una limitación importante en el uso de protección anódica es la probabilidad de que se produzcan tipos de corrosión locales en la zona del estado pasivo del metal. Para prevenir este fenómeno, según estudios preliminares, se recomienda un valor del potencial protector en el que no se produzcan tipos de corrosión locales o se introduzcan aditivos inhibidores en la solución. Por ejemplo, la protección anódica del acero 12X18N10T en soluciones de cloruro en presencia de iones NO 3 previene la formación de picaduras y reduce la velocidad de disolución del acero 2000 veces. En algunos casos, debido al mayor riesgo de procesos de corrosión local, el uso de protección anódica resulta ineficaz. Un fuerte aumento La pasivación actual de metales con temperaturas crecientes de medios agresivos limita el uso de protección anódica a temperaturas elevadas. Durante el funcionamiento estacionario de la instalación, la cantidad de corriente de polarización necesaria para mantener un estado pasivo estable cambia constantemente debido a cambios en los parámetros operativos del entorno corrosivo (temperatura, composición química, condiciones de mezcla, velocidad de la solución, etc.). El potencial de una estructura metálica se puede mantener dentro de límites específicos mediante polarización constante o periódica. En el caso de la polarización periódica, la corriente se activa y desactiva cuando se alcanza un determinado valor de potencial o cuando se desvía en cierta medida. En ambos casos, los parámetros de protección anódica se determinan experimentalmente en condiciones de laboratorio. Para utilizar con éxito la protección anódica, el objeto debe cumplir los siguientes requisitos: a) el material del aparato debe estar pasivado en el entorno tecnológico; b) el diseño del dispositivo no debe tener remaches, el número de grietas y bolsas de aire debe ser mínimo, la soldadura debe ser de alta calidad; c) el cátodo y el electrodo de referencia en el dispositivo protegido deben estar constantemente en solución. En la industria química, los dispositivos cilíndricos, así como los intercambiadores de calor, son los más adecuados para la protección anódica. Actualmente, la protección anódica de los aceros inoxidables se utiliza para tanques de medición, colectores, tanques e instalaciones de almacenamiento en la producción de ácido sulfúrico, fertilizantes minerales y soluciones de amoníaco. Se describen casos de uso de protección anódica de equipos de intercambio de calor en la producción de ácido sulfúrico y fibra artificial, así como baños para niquelado químico. El método de protección anódica tiene una aplicación relativamente limitada, ya que la pasivación es efectiva principalmente en ambientes oxidantes en ausencia de iones despasivantes activos, como los iones de cloro para hierro y aceros inoxidables. Además, la protección anódica es potencialmente peligrosa: en caso de un corte de energía, el metal puede activarse y sufrir una intensa disolución anódica. Por tanto, la protección anódica requiere un sistema de control cuidadoso. A diferencia de la protección catódica, la velocidad de corrosión con protección anódica nunca disminuye a cero, aunque puede ser muy pequeña. Pero la densidad de corriente protectora aquí es mucho menor y el consumo de electricidad es bajo. Otra ventaja de la protección anódica es su alta capacidad de disipación, es decir. la posibilidad de protección a una distancia mayor del cátodo y en áreas eléctricamente blindadas.3.3 Protección del oxígeno
Protección de oxígeno es un tipo de protección electroquímica en el que el potencial de la estructura metálica protegida se desplaza en una dirección positiva al saturar el ambiente corrosivo con oxígeno. Como resultado de esto, la velocidad del proceso catódico aumenta tanto que es posible transferir el acero del estado activo al pasivo.Figura 54 - Dependencia de la velocidad de corrosión del acero de baja aleación en agua a una temperatura de 300 °C de la concentración de oxígeno en el agua. Dado que el valor de la corriente de pasivación crítica de las aleaciones Fe-Cr, que incluyen los aceros, depende significativamente del contenido de cromo en ellos, su eficiencia aumenta al aumentar la concentración de cromo en la aleación. La protección con oxígeno se utiliza para la corrosión de equipos de energía térmica que funcionan en agua con parámetros elevados (alta temperatura y presión). En la Fig. 54 Se presenta la dependencia de la velocidad de corrosión del acero de baja aleación de la concentración de oxígeno en agua a alta temperatura. Como puede verse, un aumento en la concentración de oxígeno disuelto en agua conduce a un aumento inicial en la velocidad de corrosión, una disminución posterior y una mayor estacionariedad. Se logran bajas tasas de disolución del acero en estado estacionario (10-30 veces más bajas que aquellos sin protección) con un contenido de oxígeno en agua de ~ 1,8 g/l. La protección del oxígeno de los metales ha encontrado aplicación en energía nuclear.
4. Desarrollo y producción de nuevos.
materiales de construcción mayor resistencia a la corrosión
La mejora de las propiedades anticorrosión de los propios materiales metálicos se lleva a cabo:
- eliminación de impurezas de metales y aleaciones que aceleran los procesos de corrosión; dopaje.
5 Transición en varias estructuras de metal.
a materiales no metálicos químicamente resistentes
Los materiales no metálicos son una reserva adicional para organizar la protección anticorrosión. Los dispositivos individuales o piezas para ellos pueden estar hechos de vidrio, cerámica, vitrocerámica, plástico vinílico, faolita, grafito y otros materiales no metálicos. Su rasgo distintivo Es una alta resistencia a la corrosión en muchos ambientes agresivos. Los materiales no metálicos se analizan en detalle en el Capítulo V, Parte 4.
6 Diseño y operación racional de estructuras y piezas metálicas.
Al diseñar una producción química, por regla general, se presta especial atención al análisis de la naturaleza del entorno agresivo y las condiciones del proceso. En base a estos datos se selecciona un material con suficiente resistencia química. Sin embargo, el material estructural que sea más resistente en un ambiente corrosivo determinado no evita en todos los casos el peligro de una rápida destrucción por corrosión. Por lo tanto, el diseño racional de componentes y dispositivos individuales merece la misma atención. En muchos casos, un mal diseño puede provocar la formación de zonas estancadas, huecos, concentraciones de tensiones y otros fenómenos que contribuyen a la aparición y progresión de la corrosión. Al mismo tiempo, ya en la etapa de diseño es posible proporcionar tales Decisiones constructivas componentes individuales del dispositivo, lo que reducirá o eliminará significativamente la posibilidad del proceso de corrosión. Al diseñar equipos, se debe prestar atención a la naturaleza del tratamiento de la superficie metálica, el contacto de los elementos de conexión hechos de diferentes materiales, el modo de distribución de los flujos de refrigerante, la presencia de grietas y huecos y la posibilidad de formación de estancados. zonas. Una superficie metálica lisa tiene menos defectos en forma de rayones, irregularidades, etc. La suciedad, el polvo y otras sustancias se acumulan más fácilmente en una superficie rugosa. Esto es especialmente típico en la producción de fertilizantes y sales. En este caso, los equipos y estructuras metálicas con una superficie rugosa se cubren con varias sustancias. Si estas sustancias son higroscópicas, se adhieren a la superficie del metal, creando bolsas locales con una alta concentración de electrolito, lo que contribuye a una mayor corrosión. Si el dispositivo que se está diseñando contiene piezas hechas de diversos materiales metálicos, existe peligro de corrosión por contacto. En este caso, incluso en la etapa de diseño, se deben tomar medidas para prevenir o mitigar este fenómeno. Generalmente se utiliza una de las dos técnicas posibles. Las piezas en contacto de metales diferentes se fabrican con diferentes tamaños de superficie. En este caso, la pieza de menor superficie deberá ser de un metal más noble (casquillos de válvula, anillos de pistón bombas, etc). Si este método resulta imposible, se aíslan entre sí piezas hechas de diferentes materiales. Se debe prestar especial atención a las propiedades del material de amortiguación. Debe ser inerte respecto al entorno de trabajo y tener una alta resistencia al desgaste. Algunos materiales aislantes (fieltro, amianto, madera) pueden absorber y retener la humedad y, por tanto, ser una fuente de mayor corrosión. Algunos materiales poliméricos, sujetos a envejecimiento con el tiempo, al entrar en contacto con el agua, pueden liberar agentes corrosivos que aceleran la destrucción de los metales. Por ello, los materiales aislantes suelen estar impregnados de alquitrán o betún, y los materiales poliméricos utilizados se someten a estudios especiales para determinar el riesgo de liberación de agentes agresivos. Muchos procesos ocurren cuando temperaturas elevadas. La superficie metálica en contacto con los refrigerantes está sujeta a efectos corrosivos adicionales. Cuanto mayor es la temperatura, más intensa es la destrucción del metal. Por ejemplo, los intercambiadores de calor son uno de los tipos de equipos menos resistentes. En el 92% de los casos, la causa del fallo del intercambiador de calor es la corrosión de las superficies de transferencia de calor. Al diseñar dispositivos, es necesario prever una distribución uniforme del flujo de calor y eliminar la posibilidad de sobrecalentamiento local. En muchos dispositivos industriales en los que se producen procesos a alta temperatura, se proporcionan tales medidas. Por ejemplo, en la producción de amoníaco, se proporciona un canal entre la caja del catalizador, en la que se produce la reacción a una temperatura de 350-420ºC, y el cuerpo del aparato, por cuyo interior circula gas frío. Esta técnica de diseño protege las paredes del aparato del sobrecalentamiento. Si se utilizan reactores con camisa en un proceso químico, se debe instalar un agitador dentro del reactor para garantizar un movimiento uniforme del líquido a través de la superficie de transferencia de calor. Los serpentines, calderas y otros equipos para calentar medios de proceso deben sumergirse en líquido. Para los equipos de intercambio de calor, los tipos de corrosión más comunes son los locales, como la picadura, la grieta y la intergranular. En diseño estructural Se deben designar los lugares y métodos de soldadura. Al soldar metales, se crean grandes tensiones de tracción en la zona de soldadura y en la zona cercana al calor. En las zonas ubicadas a lo largo de la costura, donde el metal se calienta por encima de temperaturas críticas, la estructura del metal cambia. Esto puede hacer que el metal se agriete. Al diseñar conjuntos y piezas soldadas, se deben tomar una serie de medidas: evitar la acumulación de costuras, excluir la soldadura por puntos, en la que la concentración de tensiones es especialmente alta, utilizar recocido local, etc. Acumulación de humedad en diversos elementos estructurales contribuye al desarrollo de la corrosión. Por lo tanto, al crear diversas estructuras, se tiene en cuenta la posibilidad de cavidades de ventilación, la presencia de orificios de drenaje, etc. Las grietas y grietas son zonas muy peligrosas en el equipo en términos de corrosión. En ellos puede producirse una concentración de la solución de trabajo, se altera la aireación, lo que inevitablemente conducirá al desarrollo de corrosión local. Desde este punto de vista, son peligrosas las soldaduras intermitentes, en las que, debido al flojo ajuste del material entre sí, se forman grietas y huecos, que son la causa de la corrosión por grietas. La formación de zonas estancadas de líquido en aparatos y tuberías aumenta en gran medida la posibilidad de corrosión debido a la formación de microvapores de aireación desigual. Esto también se ve facilitado por la deposición de diversos sedimentos en la zona estancada. El producto no debe tener varios huecos, ranuras y ranuras en las que se pueda acumular humedad. Los elementos estructurales deben ser lo más racionalizados posible, esto facilita la evaporación de la humedad. En unidades diseñadas racionalmente, se elimina la posibilidad de acumulación de humedad y productos de corrosión, y se brinda la posibilidad de eliminar sedimentos. Existen otros requisitos de diseño que garantizan la creación de productos que sean menos susceptibles a la corrosión. Estos incluyen: requisitos para la disposición general y disposición de los elementos, teniendo en cuenta la posibilidad de aplicar y renovar varios recubrimientos durante la operación y durante las reparaciones, teniendo en cuenta las características operativas de los productos, etc.
BIBLIOGRAFÍA
Protección anódica. Uso de la pasividad en la práctica de protección contra la corrosión.
Muchos metales se encuentran en un estado pasivo en algunos ambientes agresivos. El cromo, el níquel, el titanio y el circonio pasan fácilmente a un estado pasivo y lo mantienen estable. A menudo, la aleación de un metal que es menos propenso a la pasivación con un metal que se pasiva más fácilmente conduce a la formación de aleaciones bastante bien pasivadas. Un ejemplo son las variedades de aleaciones Fe-Cr, que son diversos aceros inoxidables y resistentes a los ácidos, resistentes, por ejemplo, al agua dulce, a la atmósfera, al ácido nítrico, etc. Este uso de la pasividad en la tecnología de protección contra la corrosión se conoce desde hace mucho tiempo y tiene una gran importancia práctica. Pero recientemente ha surgido una nueva dirección en la protección de metales con oxidantes que por sí solos no son capaces de causar pasividad. Se sabe que un cambio en el potencial del metal activo en dirección negativa debería reducir la velocidad de corrosión. Si el potencial se vuelve más negativo que el de equilibrio en un ambiente dado, entonces la velocidad de corrosión debería ser cero (protección catódica, uso de protectores). Obviamente, de manera similar, pero debido a la polarización anódica de una fuente externa de energía eléctrica, es posible transferir un metal capaz de esto a un estado pasivo y así reducir la velocidad de corrosión en varios órdenes de magnitud. El consumo de energía eléctrica no debe ser grande, ya que la corriente es generalmente muy pequeña. Hay requisitos que debe cumplir un sistema para que se le pueda aplicar protección anódica. En primer lugar, es necesario conocer de forma fiable la curva de polarización anódica del metal seleccionado en un entorno agresivo determinado. Cuanto más alto yo PAG, mayor será la corriente necesaria para transferir el metal a un estado pasivo; cuanto más pequeño es nn , se requiere menos consumo de energía para mantener la pasividad; cuanto más amplio sea el rango Δφ n, mayores fluctuaciones potenciales se pueden tolerar, es decir más fácil será mantener el metal en estado pasivo. Es necesario asegurarse de que en la región Δφ n el metal se corroa uniformemente. De lo contrario, incluso con un valor pequeño de inn Es posible la formación de úlceras y la corrosión de la pared del producto. La forma de la superficie protegida puede ser bastante compleja, lo que dificulta mantener el mismo valor potencial en toda la superficie; a este respecto, es especialmente deseable un valor grande de Δφ n. Por supuesto, también se requiere una conductividad eléctrica del medio suficientemente buena. El uso de protección anódica es aconsejable en ambientes altamente agresivos, por ejemplo en la industria química. Si existe una interfaz líquido-gas, hay que tener en cuenta que en un entorno gaseoso la protección anódica no puede extenderse a la superficie del metal, lo que, sin embargo, también es típico de la protección catódica. Si la fase gaseosa también es agresiva o hay una interfaz inestable, lo que conduce a salpicaduras de líquido y a la sedimentación de gotas en el metal sobre la interfaz, si se produce una humectación periódica de la pared del producto en una zona determinada, entonces surge la cuestión de otros métodos de Se debe elevar la protección de la superficie por encima de un nivel de líquido constante. La protección anódica se puede realizar de varias formas. 1. Aplicación sencilla de una fem constante. de una fuente externa de energía eléctrica. El polo positivo está conectado al producto protegido y cerca de su superficie se colocan cátodos relativamente pequeños. Se colocan en tal cantidad y a tal distancia de la superficie protegida para asegurar una polarización anódica lo más uniforme posible del producto. Este método se utiliza si Δφ n es lo suficientemente grande y no hay peligro, con alguna inevitable distribución desigual del potencial del ánodo, activación o repasivación, es decir yendo más allá de los límites de Δφ n. De este modo se pueden proteger con ácido sulfúrico productos de titanio o circonio. Solo hay que recordar que para la pasivación, primero será necesario pasar una corriente más alta, que está asociada con la transferencia del potencial más allá de φ n. . Para el período inicial, es recomendable disponer de una fuente adicional de energía. También hay que tener en cuenta la mayor polarización de los cátodos, cuya densidad de corriente es elevada debido a su pequeño tamaño. Sin embargo, si la zona del estado pasivo es grande, una variación del potencial catódico, aunque sea de unas pocas décimas de voltio, no supone ningún peligro. Encendido y apagado periódico de la corriente de protección cuando el producto ya está pasivado. Cuando se activa la corriente del ánodo, el potencial del producto se desplaza hacia el lado negativo y puede producirse una despasivación. Pero como a veces esto sucede con bastante lentitud, una simple automatización puede garantizar que la corriente protectora se active y desactive en tiempo correcto. Cuando el potencial alcanza el valor φ nn ", es decir, antes del inicio de la repasivación, la corriente se corta; cuando el potencial se mueve negativo a φ nn (inicio de la activación), se vuelve a conectar la corriente. El desplazamiento de potencial hacia el lado del cátodo se produce cuanto más lento y menor es φ nn . Cuanto más cerca estaba el potencial del valor φ nn ", más lento se desplaza hacia el lado negativo (en la dirección de φ nn) cuando se corta la corriente. Por ejemplo, para cromo en una solución 0,1 N de H 2 SO 4 a 75 °C, si se corta la corriente a φ =0,35V, la activación se producirá en 2 horas; se corta la corriente a φ =0,6 V provoca la activación a través de 5 h; el apagado a φ = 1,05 V aumenta el tiempo de inicio de la activación a más de 127 horas. gran momento , necesario para la despasivación, permite importantes interrupciones en el suministro actual. Entonces una misma instalación puede servir para varios objetos. La dependencia del tiempo de pasivación del potencial de conmutación se explica fácilmente utilizando el concepto de fase de óxido (se forma una capa de óxido más gruesa, cuya disolución tarda más). Es más difícil explicar este fenómeno por la desorción del oxígeno pasivante. Por supuesto, al aumentar el potencial positivo, la fuerza de unión en la capa de adsorción debería aumentar. Pero cuando se activa la corriente, la descarga de la doble capa se produce relativamente rápido, aunque la capa de adsorción puede persistir durante mucho tiempo. 3. Si la región del estado pasivo (Δφ nn) es pequeña, entonces es necesario utilizar un potenciostato que mantenga un valor de potencial determinado (en relación con un determinado electrodo de referencia) dentro de límites estrechos. El potenciostato debe ser capaz de entregar alta corriente. Actualmente ya existen una serie de instalaciones de protección anódica implementadas a escala industrial. También están protegidos los productos fabricados con acero al carbono ordinario. Con la protección anódica, la vida útil del equipo no solo aumenta, sino que también se reduce la contaminación del ambiente agresivo con productos de corrosión. Por ejemplo, en el oleum, el acero al carbono se corroe muy lentamente y en este sentido no necesita protección. Pero en los recipientes donde se almacena este producto se contamina con hierro. Así, sin protección anódica en una de las instalaciones industriales, el contenido de hierro en oleum era ~0,12%. Después de aplicar la protección, la concentración de hierro disminuyó a ~0,004%, lo que corresponde a su contenido en el producto original. La contaminación de los productos de la industria química con impurezas de compuestos metálicos, que es consecuencia de la corrosión de los equipos, es en muchos casos muy indeseable e incluso inaceptable. Sin embargo, el uso de protección anódica presenta importantes dificultades. Mientras que la protección catódica se puede utilizar para proteger muchos metales sumergidos en cualquier medio eléctricamente conductor, como sólido o líquido, la protección anódica se utiliza sólo para proteger secciones enteras de plantas químicas que están hechas de metal que puede pasivarse en el entorno de trabajo. Esto es precisamente lo que limita su uso. Además, la protección anódica es potencialmente peligrosa, ya que si se interrumpe el suministro de corriente sin restablecer inmediatamente la protección, comenzará una disolución muy rápida en la zona en cuestión, ya que una rotura en la película forma un camino de baja resistencia en condiciones de polarización anódica. del metal. El uso de protección anódica requiere un diseño cuidadoso de la planta química. Estos últimos deberán disponer de un sistema de seguimiento que permita llamar inmediatamente la atención del operador ante cualquier pérdida de protección. Para ello puede ser suficiente sólo un aumento local de la corriente del ánodo, pero en peor de los casos Es posible que sea necesario vaciar toda la instalación inmediatamente. La protección anódica no proporciona resistencia en presencia de iones agresivos. Así, los iones cloruro destruyen la película pasiva y, por tanto, es necesario mantener baja su concentración, a excepción de la protección del titanio, que puede pasivarse en ácido clorhídrico. En condiciones de protección anódica, los electrolitos tienen una buena capacidad de disipación y por lo tanto se requiere un número relativamente pequeño de electrodos para mantener su protección establecida. Sin embargo, a la hora de diseñar instalaciones de protección anódica se debe tener en cuenta que en las condiciones previas a la pasivación la capacidad de disipación es peor. La protección anódica consume muy poca energía y se puede utilizar para proteger metales estructurales comunes que se pueden pasivar, como el carbono y el acero inoxidable, en muchos entornos. Esta protección se controla y mide fácilmente y no requiere un costoso tratamiento de la superficie metálica, ya que aprovecha el efecto de reacción espontánea entre las paredes de los contenedores y su contenido. El método es elegante y es probable que su uso se amplíe una vez que se superen las dificultades de medición y control.Recubrimientos como método de protección de los metales contra la corrosión.
La protección de los metales, basada en cambios en sus propiedades, se lleva a cabo mediante un tratamiento especial de su superficie o mediante aleación. El tratamiento de la superficie del metal para reducir la corrosión se lleva a cabo de una de las siguientes maneras: cubriendo el metal con películas pasivadoras de la superficie de sus compuestos poco solubles (óxidos, fosfatos, sulfatos, tungstatos o combinaciones de los mismos), creando capas protectoras a partir de lubricantes. , betún, pinturas, esmaltes, etc. P. y aplicando recubrimientos de otros metales más resistentes en estas condiciones específicas que el metal a proteger (estañado, galvanizado, cobreado, niquelado, cromado, plomo, rodiado, etc.). El efecto protector de la mayoría de las películas superficiales se puede atribuir al aislamiento mecánico del metal del entorno que provocan. Según la teoría de los elementos locales, su efecto debe considerarse como resultado de un aumento resistencia eléctrica(Figura 8). Un aumento en la estabilidad de los productos de hierro y acero cuando su superficie está recubierta con depósitos de otros metales se debe tanto al aislamiento mecánico de la superficie como a un cambio en sus propiedades electroquímicas. En este caso, ya sea un cambio en el potencial reversible de la reacción anódica hacia valores más positivos (recubrimiento con cobre, níquel, rodio) o un aumento en la polarización de la reacción catódica: un aumento en la sobretensión de hidrógeno (zinc , estaño, plomo). Como muestran los diagramas, todos estos cambios reducen la velocidad de corrosión. El tratamiento de superficies metálicas se utiliza para proteger maquinaria, equipos, aparatos y artículos del hogar para protección temporal durante el transporte, almacenamiento y conservación (lubricantes, películas pasivadoras) y para protección a más largo plazo durante su operación (barnices, pinturas, esmaltes, revestimientos metálicos). Una desventaja común de estos metales es que cuando se elimina la capa superficial (por ejemplo, debido al desgaste o daño), la velocidad de corrosión en el área dañada aumenta drásticamente y no siempre es posible volver a aplicar la capa protectora. En este sentido, la aleación es un método mucho más eficaz (aunque más caro) para aumentar la resistencia a la corrosión de los metales. Un ejemplo de aumento de la resistencia a la corrosión de un metal mediante aleación son las aleaciones de cobre y oro. Para proteger de manera confiable el cobre, es necesario agregarle una cantidad significativa de oro (al menos 52,2 % at.%). Los átomos de oro protegen mecánicamente a los átomos de cobre de su interacción con el medio ambiente. Para aumentar la estabilidad del metal se necesita una cantidad incomparablemente menor de componentes de aleación, si estos componentes son capaces de formar películas pasivadoras protectoras con oxígeno. Por lo tanto, la introducción de cromo en una cantidad de varios por ciento aumenta drásticamente la resistencia a la corrosión.Inhibidores.
La velocidad de corrosión también se puede reducir cambiando las propiedades del entorno corrosivo. Esto se consigue mediante un tratamiento adecuado del medio ambiente, con lo que se reduce su agresividad, o introduciendo en el entorno corrosivo pequeños aditivos de sustancias especiales, los llamados retardadores o inhibidores de la corrosión. El tratamiento del medio ambiente incluye todos los métodos que reducen la concentración de sus componentes, especialmente aquellos que son corrosivos. Por ejemplo, en ambientes de sal neutra y agua dulce, uno de los componentes más agresivos es el oxígeno. Se elimina mediante desaireación (ebullición, destilación, burbujeo de gas inerte) o se lubrica con reactivos adecuados (sulfitos, hidracina, etc.). Una disminución en la concentración de oxígeno debería reducir casi linealmente la corriente límite de su reducción y, en consecuencia, la tasa de corrosión del metal. La agresividad del medio también disminuye cuando se alcaliniza, se reduce el contenido total de sal y se sustituyen los iones más agresivos por otros menos agresivos. Cuando se realiza un tratamiento anticorrosión del agua para reducir la formación de incrustaciones, se utiliza ampliamente su purificación con resinas de intercambio iónico. Los inhibidores de corrosión se dividen, según las condiciones de su uso, en fase líquida y fase vapor o volátiles. Los inhibidores de fase líquida se dividen a su vez en inhibidores de corrosión en ambientes neutros, alcalinos y ácidos. Las sustancias inorgánicas aniónicas se utilizan con mayor frecuencia como inhibidores de soluciones neutras. Su efecto inhibidor aparentemente está asociado con la oxidación de la superficie del metal (nitritos, cromatos) o con la formación de una película de un compuesto poco soluble entre el metal, este anión y, posiblemente, oxígeno (fosfatos, hidrofosfatos). La excepción a este respecto son las sales del ácido benzoico, cuyo efecto inhibidor está asociado principalmente a fenómenos de adsorción. Todos los inhibidores de medios neutros inhiben predominantemente la reacción anódica, desplazando el potencial estacionario en una dirección positiva. Hasta la fecha todavía no se han podido encontrar inhibidores eficaces de la corrosión de metales en soluciones alcalinas. Sólo los compuestos de alto peso molecular tienen algún efecto inhibidor. Como inhibidores de la corrosión ácida se utilizan casi exclusivamente sustancias orgánicas que contienen nitrógeno, azufre u oxígeno en forma de grupos amino, imino, tio, así como grupos carboxilo, carbonilo y algunos otros. Según la opinión más común, el efecto de los inhibidores de corrosión ácidos está asociado con su adsorción en la interfaz metal-ácido. Como resultado de la adsorción de inhibidores se observa inhibición de los procesos catódicos y anódicos, reduciendo la velocidad de corrosión. El efecto de la mayoría de los inhibidores de corrosión ácidos se ve reforzado por la introducción simultánea de aditivos de aniones tensioactivos: haluros, sulfuros y tiocianatos. Los inhibidores de la fase de vapor se utilizan para proteger máquinas, aparatos y otros productos metálicos durante su funcionamiento en atmósfera de aire, durante el transporte y el almacenamiento. Los inhibidores de la fase de vapor se introducen en transportadores, en materiales de embalaje o se colocan muy cerca de la unidad operativa. Debido a la presión de vapor suficientemente alta, los inhibidores volátiles alcanzan la interfaz metal-aire y se disuelven en la película de humedad que cubre el metal. Luego son adsorbidos de la solución sobre la superficie del metal. Los efectos inhibidores en este caso son similares a los observados con el uso de inhibidores de fosfato líquido. Como inhibidores en fase de vapor se utilizan habitualmente aminas de bajo peso molecular, en las que se introducen grupos apropiados, por ejemplo NO 2 o CO 2. Debido a las peculiaridades del uso de inhibidores en fase de vapor, se les imponen mayores requisitos en cuanto a su toxicidad. La inhibición es una defensa compleja y su aplicación exitosa en una variedad de entornos requiere un conocimiento amplio.Protección protectora y protección eléctrica.
La protección protectora se utiliza en los casos en que se protege una estructura (tubería subterránea, casco de barco) ubicada en un ambiente de electrolitos (agua de mar, agua subterránea, agua del suelo, etc.). La esencia de dicha protección es que la estructura está conectada a la banda de rodadura; más metal activo que el metal de la estructura protegida. El magnesio, el aluminio, el zinc y sus aleaciones se suelen utilizar como protectores a la hora de proteger productos de acero. Durante el proceso de corrosión, el protector sirve como ánodo y se destruye, protegiendo así la estructura de la destrucción. A medida que los protectores se deterioran, se sustituyen por otros nuevos. La protección eléctrica también se basa en este principio. La estructura, situada en el entorno del electrolito, también está conectada a otro metal (normalmente un trozo de hierro, un riel, etc.), pero a través de una fuente de corriente externa. En este caso, la estructura protegida está conectada al cátodo y el metal está conectado al ánodo de la fuente de corriente. Una fuente de corriente quita electrones del ánodo, el ánodo (metal protector) se destruye y el agente oxidante se reduce en el cátodo. ¡La protección eléctrica tiene ventajas sobre la protección de la banda de rodadura! el radio de acción del primero es de unos 2000 m, el segundo de unos 50 m Cambios en la composición del medio ambiente. Para frenar la corrosión de los productos metálicos, se utilizan sustancias (la mayoría de las veces orgánicas) llamadas inhibidores de corrosión o inhibidores. Se utilizan en los casos en los que es necesario proteger el metal de la corrosión por ácidos. Los científicos soviéticos han creado una serie de inhibidores (preparaciones de los grados ChM, PB, etc.) que, cuando se añaden al ácido, ralentizan la disolución (corrosión) de los metales cientos de veces. EN últimos años Se han desarrollado inhibidores volátiles (o atmosféricos). Impregnan papel que se utiliza para envolver productos metálicos. Los vapores del inhibidor se absorben en la superficie del metal y forman una película protectora sobre ella. Los inhibidores se utilizan ampliamente en la descalcificación química de calderas de vapor, la eliminación de incrustaciones de productos procesados, así como durante el almacenamiento y transporte de ácido clorhídrico en contenedores de acero. Los inhibidores inorgánicos incluyen nitritos, cromatos, fosfatos y silicatos. El mecanismo de acción de los inhibidores es objeto de investigación por parte de muchos químicos.Creación de aleaciones con propiedades anticorrosión.
Introduciendo hasta un 12% de cromo en la composición del acero se obtiene acero inoxidable resistente a la corrosión. Las adiciones de níquel, cobalto y cobre mejoran las propiedades anticorrosivas del acero, ya que aumenta la susceptibilidad de las aleaciones a la pasivación. La creación de aleaciones con propiedades anticorrosión es una de las áreas importantes en la lucha contra las pérdidas por corrosión.Metas, objetivos y métodos de investigación.
Objetivo dado trabajo de investigación es el estudio de la corrosión y restauración de los valores arquitectónicos de la ciudad de Tsivilsk y la administración rural de Ivanovo. En base al objetivo se planteó lo siguiente: tareas:Analizar la literatura sobre este tema.
Métodos de estudio para proteger productos metálicos de la corrosión.
Realizar un estudio para identificar los valores arquitectónicos de la ciudad de Tsivilsk y la administración rural de Ivanovo.
Sugerir formas de proteger los objetos en estudio.
- Recopilación y análisis de información teórica. Búsqueda de monumentos culturales: monumentos, placas conmemorativas, etc. Observaciones para determinar el material del que está elaborado el valor arquitectónico y posibles procesos de destrucción.
Resultados de la investigacion
De noviembre a diciembre de 2005 se llevó a cabo una investigación sobre los valores arquitectónicos de la ciudad de Tsivilsk y la administración rural de Ivanovo. Durante el recorrido por Tsivilsk se identificaron las siguientes atracciones:- Monumento dedicado al 400 aniversario de la ciudad de Tsivilsk. Monumento a los soldados caídos en Velikaya guerra patriótica. Monumento a V. I. Lenin. Exposición frente a la Comisaría Militar Distrital. Monumento en honor del participante de la Segunda Guerra Mundial, residente de Tsivilsk A. Rogozhkin. Monumento en honor del participante de la Segunda Guerra Mundial, residente de Tsivilsk Silantiev. Exposición frente al jardín de infancia nº 4.
Valor arquitectónico | Apariencia(material, forma) | Métodos de protección contra la corrosión. |
||
llevado a cabo | el mas optimo |
|||
Tsivilsk | Monumento dedicado al 400 aniversario de Tsivilsk | |||
Monumento a VI Lenin | Un Lenin de mármol con el brazo extendido, cubierto con pintura plateada, está instalado sobre un soporte de hormigón de aproximadamente 1 metro de altura. La altura total de la composición es de unos 2,5-3 metros. | Pintura periódica del monumento, incluido el pedestal. Sin embargo, esto no protege contra daños mecánicos bajo la influencia del viento, el agua y el sol. Hay una grieta notable en la pierna. | Se requieren trabajos de restauración para eliminar la grieta. Es recomendable utilizar pinturas alquídicas especiales para aplicar sobre la superficie del monumento. | |
Su arquitectura y material son similares al monumento a Lenin. La composición incluye un soldado realizado en mármol, cubierto con pintura plateada, ubicado sobre un soporte de hormigón de 1 metro de altura. El stand está revestido con láminas de metal. La altura total es de unos 5 metros. Cerca hay una placa conmemorativa, que es una larga pared de ladrillos en la que están montadas láminas galvanizadas con los nombres de los participantes de la Segunda Guerra Mundial que no regresaron del frente. | La pintura se realiza, sin embargo, debido a la gran altura del monumento, no se realiza con regularidad. No se corroe. | Es necesario limpiar el monumento de hojas y ramas secas. | ||
Exposición ante la Comisaría Militar Distrital | Un cañón montado sobre un soporte de ladrillo. La altura es de unos 2 metros. Metal (acero), verde. En el cañón del arma hay una muesca de 4 cm de profundidad. | Los trabajadores de la comisaría pintan regularmente el arma con pintura alquídica verde, aunque en un tono ligeramente diferente al color original del producto. Una muesca en el tronco contribuye a la destrucción. | Es posible proteger la banda de rodadura; como protector se pueden utilizar remaches y placas de zinc. |
|
Monumento en honor del participante de la Segunda Guerra Mundial, residente de Tsivilsk A. Rogozhkin | Hay una losa de mármol verde sobre una base de hormigón. En la losa está montado un bajorrelieve hecho de una aleación resistente a la corrosión con la imagen del marinero Silantiev. | La restauración del monumento no se ha llevado a cabo desde hace mucho tiempo. Se ven grietas en la losa de mármol. El bajorrelieve no se corroe, pero se notan las piezas desconchadas. | Cuidado y reemplazo oportuno de las losas de mármol, que son más susceptibles a la destrucción. |
|
Monumento en honor del participante de la Segunda Guerra Mundial, residente de Tsivilsk Silantiev | Similar al monumento en honor a Rogozhkin. Un bajorrelieve hecho de una aleación duradera con la imagen de Silantyev está montado sobre un soporte de mármol en forma de triángulo. | El bajorrelieve no está sujeto a corrosión. | Recubrimiento oportuno de estructuras portantes con compuestos protectores. | |
Exposición frente al jardín de infancia nº 4. | Estatuas de dos pioneros con cornetas. | |||
n. experimentado | Monumento a los soldados caídos en la Gran Guerra Patria | En la pared de ladrillo blanco hay un bajorrelieve que representa soldados en guerra, pintado con pintura dorada. | No se corroe. Pintado regularmente. Se notan grietas en el bajorrelieve. | Reparando la grieta. |
Con. Ivánovo | Placa conmemorativa a los soldados caídos en la Gran Guerra Patria | |||
Pueblo de Sinya-Kotyaki | Monumento en honor al 60 aniversario de la Victoria en la Gran Guerra Patria (erigido en julio de 2004). | El monumento está hecho de virutas de mármol, revestido con ladrillo blanco. Las inscripciones del monumento están pintadas de oro. | Prácticamente no está sujeto a corrosión. El ladrillo puede ser destruido por el viento, el sol y el agua. | Pintura de letras más regular, reemplazo oportuno de estructuras de soporte. |
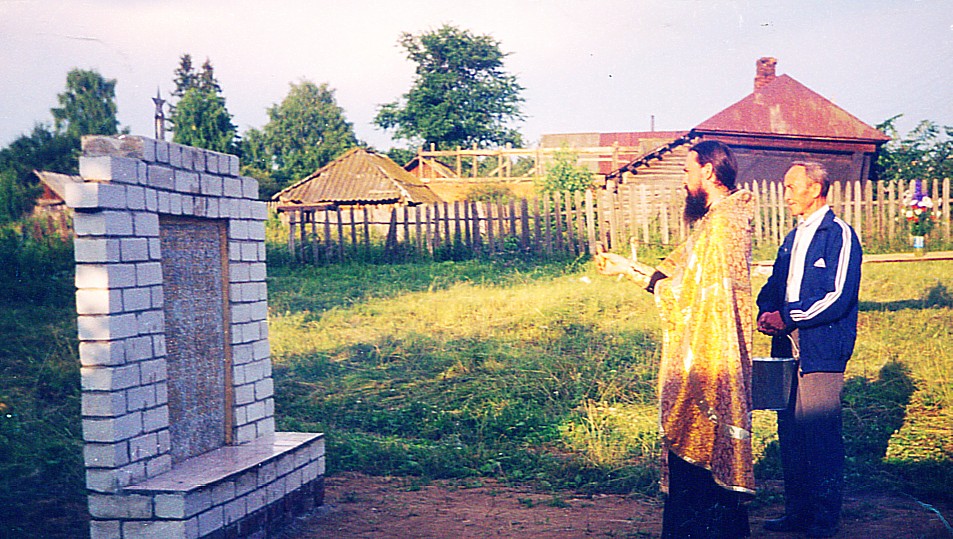
conclusiones
Como resultado del estudio de los valores arquitectónicos de la ciudad de Tsivilsk y de la administración rural de Ivanovo, recibimos información importante sobre el estado de los monumentos y los métodos de conservación.Oxidación espontánea de metales, perjudicial para la salud. práctica industrial(reduciendo la durabilidad de los productos) se llama corrosión. El ambiente en el que se corroe el metal se llama corrosivo o agresivo.
Hay muchas formas de proteger los metales de la corrosión. Los más eficaces son la protección, la inhibición, la creación de una capa protectora (barnices, pinturas, esmaltes) y las aleaciones anticorrosión.
Se han identificado seis atracciones principales en la ciudad de Tsivilsk. Cada asentamiento estudiado de la administración rural de Ivanovo contiene un valor arquitectónico dedicado a la Gran Guerra Patria. En general, estos monumentos son composiciones complejas realizadas en mármol con la adición de fragmentos de metal. Sólo el cañón que se encuentra frente a la comisaría militar regional está expuesto a la corrosión.
Para proteger los objetos en estudio de la corrosión, se recomienda un cuidado y limpieza oportunos; para algunos (el monumento a Lenin, el monumento en honor a los soldados caídos en Tsivilsk) se recomienda pintarlos regularmente con compuestos especiales. El monumento en honor al marinero Rogozhkin requiere la restauración de la estructura de soporte. Para el arma más susceptible a la corrosión, también ofrecemos protección de la banda de rodadura.
Lista de literatura usada
- Akhmetov N.S., Química general e inorgánica. - M.: Escuela de posgrado, 1989 Nekrasov B.V., Libro de texto de química general. - M.: Química, 1981 Cotton F., Wilkinson J., Fundamentos de química inorgánica. - M.: Mir, 1979 Karapetyants M.Kh., Drakin S.I., Química general e inorgánica. - M.: Química, 1993 Yakovlev A. A. En el mundo de la piedra. M.: Detgiz, 1991
1 Del latín corroer - corroer.