Al bombear petróleo a través de un oleoducto principal, la presión desarrollada por las bombas de las estaciones de bombeo se gasta en la fricción del líquido contra la pared de la tubería h , superando la resistencia local h ms, resistencia estática debido a la diferencia en las marcas geodésicas (nivelación) z, además de crear la presión residual requerida en el extremo de la tubería. .
La pérdida total de presión en la tubería será
H = h + h ms + z + h reposo. (1.10)
Las pérdidas de presión debidas a la resistencia local son del 1 al 3% de las pérdidas lineales. Entonces la expresión (1.10) tomará la forma
H = 1.02h + z + h descanso. (1.11)
La presión residual hres es necesaria para superar la resistencia de las comunicaciones tecnológicas y llenar los depósitos del punto final. La pérdida de presión por fricción en la tubería se determina mediante la fórmula de Darcy-Weisbach.
o según la fórmula generalizada de Leibenzon
, (1.13)
donde L p es la longitud estimada del oleoducto;
w – velocidad media flujo de petróleo a través del oleoducto;
– viscosidad cinemática calculada del aceite;
– coeficiente de resistencia hidráulica;
, m – coeficientes de la fórmula generalizada de Leibenzon.
Los valores de , y m dependen del régimen de flujo del fluido y de la rugosidad de la superficie interior de la tubería. El régimen de flujo de fluido se caracteriza por el parámetro de Reynolds adimensional.
, (1.14)
Pendiente hidráulica
La pendiente hidráulica es la pérdida de presión por fricción por unidad de longitud de la tubería.
(1.15)
Teniendo en cuenta (1.15), la ecuación (1.11) toma la forma
9 Determinación del punto de transferencia y longitud estimada del oleoducto.
punto de paso Este es el nombre que se le da a una colina en la ruta del oleoducto desde donde el petróleo llega al punto final del oleoducto por gravedad. En el caso general, puede haber varios vértices de este tipo. La distancia desde el inicio del oleoducto hasta el más cercano se llama longitud estimada del oleoducto. Consideremos esto usando el ejemplo de un oleoducto con longitud L, diámetro D y productividad Q.
.
Desde el punto a, perpendicularmente hacia arriba, trazamos un segmento ac igual al valor de h l en la escala de altura.
Al conectar los puntos b y c, obtenemos el triángulo abc, también llamado triángulo hidráulico. Su hipotenusa bc determina la posición de la línea de pendiente hidráulica en las escalas seleccionadas.
El punto donde la línea 2 toca la línea del perfil indica la posición del punto de silla, que determina la longitud estimada del oleoducto.
Esto sugiere que basta con bombear petróleo hasta el punto de transferencia para que llegue al punto final del oleoducto con el mismo caudal. El flujo de aceite por gravedad está asegurado, ya que la presión disponible (z PT – z K – h OT) es mayor que la presión requerida para superar la resistencia en el tramo desde el punto de paso hasta el punto final.
(z PT – z K – h OT)>i∙(L– l PT) ,
donde l PT es la distancia desde el punto de partida del oleoducto hasta el punto de transferencia.
En este caso, la distancia L P =l PT se toma como longitud de diseño de la tubería, y la diferencia de elevaciones geodésicas se toma igual a z= z PT – z H . Si no hay intersección de la línea de pendiente hidráulica con el perfil, entonces la longitud estimada de la tubería es igual a su longitud total L P = L, y z = z K – z H.
10. Para un oleoducto principal de diámetro constante con n estaciones de bombeo, ecuación de equilibrio La presión tiene la forma.
Al inicio de cada tramo operativo, las subestaciones están equipadas con bombas de refuerzo. Al final de la tubería y en cada tramo operativo, es necesario proporcionar una presión residual h OST para superar la resistencia de las tuberías de proceso y el bombeo a los tanques.
El lado derecho de la ecuación (1.34) representa la pérdida de presión total en la tubería, es decir, N. En el caso de inserciones o bucles a lo largo de la ruta, el lado derecho de la ecuación (1.34) está determinado por la fórmula (1.32).
El lado izquierdo de la ecuación (1.34) es la presión total desarrollada por todas las bombas en funcionamiento de las estaciones de bombeo (presión activa). Utilizando los coeficientes de las características de la bomba, la presión total activa se puede representar mediante la relación
a P, b P, h P – coeficientes característicos y presión desarrollada por la bomba de refuerzo cuando suministra Q;
Y
,
(1.36)
Expresando el lado izquierdo de la ecuación (1.34) hasta (1.35) y el lado derecho hasta (1.30), obtenemos la ecuación de equilibrio de presiones en forma analítica.
. (1.38)
Si en el caso general hay bucles e inserciones en la parte lineal, la ecuación (1.38) tomará la forma
.
(1.39)
11 El punto de intersección de las características se denomina punto de operación (A), que caracteriza la pérdida de presión en el oleoducto y su rendimiento en determinadas condiciones de bombeo (Fig. 1.12). La igualdad de la presión creada y gastada, así como la igualdad del suministro de la bomba y el flujo de aceite en el oleoducto, llevan a una conclusión importante: el oleoducto y las estaciones de bombeo constituyen un único sistema hidráulico. Cambiar el modo de funcionamiento de la subestación (apagar algunas bombas o estaciones) conducirá a un cambio en el modo de funcionamiento del oleoducto en su conjunto. Un cambio en la resistencia hidráulica de una tubería o de su tramo individual (cambio de viscosidad, inclusión de líneas de reserva, reemplazo de tuberías en ciertos tramos de la ruta, etc.) afectará, a su vez, el modo de funcionamiento de todas las estaciones de bombeo.
(trabajo de laboratorio nº 6)
INFORMACIÓN GENERAL
Al realizar cálculos hidráulicos de tuberías de agua, intercambiadores de calor, sistemas tecnológicos de estaciones de bombeo, sistemas de recolección y tratamiento de agua, es necesario determinar las pérdidas de energía específicas (energía por unidad de peso de líquido). Las pérdidas de energía específicas (pérdidas de presión) son causadas por la fricción del líquido contra las paredes de la tubería, la fricción que se produce entre las capas de líquido en movimiento, así como su mezcla. Como lo demuestran los estudios teóricos, confirmados por la experiencia, las pérdidas de presión cuando el líquido se mueve a través de una tubería dependen del modo de movimiento del líquido (número de Reynolds Re), el diámetro, la longitud de la tubería, la rugosidad de la tubería y la velocidad de el líquido. Estas pérdidas se determinan mediante la fórmula de Darcy:
donde l es el coeficiente de Darcy (coeficiente de resistencia hidráulica);
l – longitud de la tubería;
d – diámetro interno de la tubería;
V – velocidad media del movimiento del líquido en la tubería;
g – aceleración de caída libre.
Es fácil ver que para determinar la pérdida de presión a lo largo, es necesario conocer el valor de l. En términos físicos, l significa qué parte de la presión de velocidad (V 2 /2q) es la pérdida por unidad de longitud relativa de la tubería (l/d).
Con un flujo laminar isotérmico uniforme de líquido en una tubería de sección transversal circular, el coeficiente de Darcy está determinado por la fórmula teórica de Stokes.
Por las mismas condiciones régimen turbulento flujo de fluido, el coeficiente de Darcy se calcula utilizando fórmulas empíricas y semiempíricas obtenidas sobre la base de estudios teóricos y experimentales. Estos estudios demostraron que a medida que aumenta el número de Re, el grado de influencia sobre l disminuye y el grado de influencia de la rugosidad aumenta. La explicación física de este fenómeno se basa en la hipótesis de Prandtl. De acuerdo con esta hipótesis, el flujo turbulento se puede dividir en dos regiones (Fig. 4): una subcapa viscosa (1), ubicada en la pared interior de la tubería (2), y un núcleo turbulento en su centro (3). .
El flujo de fluido en una subcapa viscosa se forma bajo la influencia de la interacción de fuerzas externas con fuerzas viscosas. Los flujos en un núcleo turbulento, según Prandtl, se producen bajo la influencia de la interacción de fuerzas externas con la fuerza de fricción que aparece debido a la mezcla.
Arroz. 4
El espesor de la subcapa viscosa δ en función de la velocidad de movimiento se calcula mediante la fórmula:
De la dependencia (15) se desprende claramente que cuanto mayor es la velocidad del flujo del fluido, menor (en igualdad de condiciones) será el espesor de la subcapa viscosa. A bajas velocidades (números de Reynolds bajos), aumenta el espesor de la subcapa viscosa. Se vuelve más grande que las protuberancias rugosas de la máquina de tubos interna y no afectan el flujo en el núcleo y l.
A altas velocidades (altos números de Reynolds), el espesor de la subcapa viscosa es pequeño. Las protuberancias de rugosidad que no están cubiertas por una subcapa viscosa tienen un efecto directo sobre el flujo en el núcleo, determinando el valor del coeficiente l. Por lo tanto, dependiendo de la relación entre las protuberancias de rugosidad D y el espesor de la subcapa viscosa δ en las tuberías, se dividen en hidráulicamente lisas (D< δ в) и гидравлически шероховатые (D >δc). Teniendo en cuenta la fórmula (3), se puede argumentar que la misma tubería puede ser hidráulicamente lisa y hidráulicamente rugosa. Esto significa que el coeficiente l será diferente para tuberías hidráulicamente lisas y rugosas.
Los experimentos muestran que, dependiendo de la relación entre D y δ en un flujo de fluido turbulento, se observan tres leyes de fricción. Cada uno de ellos es válido sólo en una determinada región de variación del número de Reynolds.
En el flujo de fluido turbulento, se distinguen tres zonas de fricción: lisa, mixta y rugosa, determinadas por la relación entre el tamaño de las protuberancias de rugosidad y el diámetro de la tubería. Dado que la resistencia al flujo de fluido depende no sólo de la altura de las protuberancias, sino también de su forma, posición relativa, número de protuberancias por unidad de área y otros factores, el concepto de rugosidad "equivalente" (Ke), determinado experimentalmente, es presentado.
La zona de fricción suave comienza con el número de Reynolds (3,5 – 4) × 10 3 y termina en su primer valor límite (Re’), determinado por la fórmula
donde es la rugosidad equivalente relativa igual a K e /d.
El coeficiente de Darcy en esta zona de fricción está determinado por la fórmula de Blasius.
(17)
La zona de fricción mixta comienza en el primer límite del número de Reynolds Re’ y termina en el segundo Re” = 500/. En esta zona de fricción, para determinar el coeficiente de Darcy, se puede utilizar la fórmula de A.L. Altshulya
. (18)
En la zona de fricción rugosa, el número de Reynolds es mayor que el segundo valor límite Re” > 500/ . En esta zona, el valor 68/Re se vuelve insignificante en comparación con , la fórmula de Altschul se convierte en la fórmula de Shifrinson
L = 0,11 × ()0,25, (19)
válido para Re > Re” y £ 0,007.
Si Re > Re” y > 0,007, el coeficiente de Darcy se calcula utilizando la fórmula de Prandtl – Nikuradze
(20)
Dado que en la zona de fricción rugosa el coeficiente de Darcy está determinado únicamente por la rugosidad relativa equivalente, la fórmula (19, 20) también sirve para encontrar .
Los valores de rugosidad equivalente se dan en la literatura de referencia sobre hidráulica. Las tablas de valores se elaboran sobre la base de datos experimentales, teniendo en cuenta el material, el método de fabricación y el estado de las tuberías. Se tiene en cuenta el estado de las tuberías: limpieza, vida útil, presencia de corrosión.
En consecuencia, teniendo datos sobre la rugosidad equivalente de las paredes de la tubería y conociendo su diámetro, es posible determinar las condiciones límite de los números de Reynolds y la zona de fricción.
Además de las condiciones consideradas de los métodos analíticos para determinar el coeficiente de Darcy, también existen dependencias gráficas de l con Re y K e. para acero tubos técnicos Estos gráficos se basan en los resultados de estudios experimentales realizados en nuestro país por G.A. Murin.
Para condiciones específicas, el coeficiente se puede determinar experimentalmente.
OBJETIVO DEL TRABAJO
Dominar los métodos experimentales y computacionales para determinar la pérdida de presión debido a la fricción a lo largo.
Consideremos tipos resistencia hidráulica .
Cuando un fluido se mueve, parte de la presión se gasta en superar diversas resistencias. Las pérdidas hidráulicas dependen principalmente de la velocidad de movimiento, por lo que la presión se expresa en fracciones de la altura de velocidad.
Dónde - coeficiente de resistencia hidráulica, que muestra qué proporción de la carga de velocidad será la presión perdida,
o en unidades de presión:
Esta expresión es conveniente porque incluye un coeficiente de proporcionalidad adimensional, llamado coeficiente de arrastre, y la presión de velocidad, que se incluye en la ecuación de Bernoulli. Por tanto, el coeficiente es la relación entre la presión perdida y la presión de velocidad.
Las pérdidas de presión durante el movimiento de un fluido son causadas por resistencias de dos tipos: resistencia a lo largo, determinada por fuerzas de fricción, y resistencia local, causada por cambios en la velocidad del flujo en dirección y magnitud.
Pérdidas locales Las energías son causadas por la llamada resistencia local: cambios locales en la forma y tamaño del canal, que provocan la deformación del flujo. Cuando un fluido fluye a través de resistencias locales, su velocidad cambia y suelen aparecer vórtices.
Ejemplos de resistencias locales incluyen los siguientes dispositivos: válvula, diafragma, codo, válvula, etc. (Fig. 37).
La presión perdida para superar la resistencia local en unidades lineales está determinada por la fórmula:
(esta expresión a menudo se llama fórmula de Weisbach),
y en unidades de presión:
donde: – coeficiente de resistencia local, generalmente determinado experimentalmente (los valores de los coeficientes se dan en los libros de referencia según el tipo y diseño de la resistencia local),
– gravedad específica del líquido,
– densidad del fluido,
V– velocidad media en la tubería en la que está instalada esta resistencia local.
Válvula de compuerta Codo Ramificación de flujo
Restricción de válvula Fusión de flujos
Válvula de expansión de diafragma con malla
Figura 37 – Ejemplos de resistencia hidráulica local
Figura 38 - Selección de la velocidad de diseño.
Si el diámetro de la tubería cambia, por lo tanto, la velocidad en ella cambia en una sección corta, entonces es más conveniente tomar la mayor de las velocidades como la velocidad de diseño al calcular (Fig. 38). Por ejemplo, un estrechamiento repentino de la tubería, entrada a la tubería, etc. ( , se toma la velocidad de diseño V = V 2).
Pérdidas por fricción o resistencias lineales son causadas por fuerzas de fricción que surgen a lo largo de toda la longitud del flujo de fluido cuando Movimiento uniforme, por lo que aumentan en proporción a la longitud del flujo. Este tipo de pérdida se produce por la fricción interna del líquido, por lo que se produce no sólo en tuberías rugosas, sino también en tuberías lisas.
La pérdida de presión debido a la fricción (a lo largo) se puede determinar mediante la fórmula:
Sin embargo, es más conveniente asociar el coeficiente con la longitud relativa. L/d. Tomemos una trama tubo redondo longitud igual a su diámetro d y denotamos el coeficiente de su resistencia, incluido en la fórmula, por . Luego para toda la longitud de la tubería l y diámetro d el coeficiente estará en L/d veces más, a saber:
¿Dónde está el coeficiente de fricción hidráulica, o coeficiente de Darcy?
l– longitud de la sección,
d- diámetro de la tubería.
Este reemplazo nos permite llevar la fórmula a una forma muy conveniente para uso práctico:
La fórmula suele denominarse fórmula de Darcy-Weisbach. El coeficiente de fricción λ en la mayoría de los casos se determina experimentalmente según el criterio de Reynolds. Re y calidad de la superficie (rugosidad).
Adición de pérdidas de carga.
En muchos casos, cuando los fluidos se mueven en diferentes sistemas hidráulicos(por ejemplo, tuberías) se producen simultáneamente pérdidas de presión por fricción a lo largo de la longitud y pérdidas locales. La pérdida total de presión en tales casos se determina como suma aritmética pérdidas de todo tipo.
Al determinar las pérdidas en todo el flujo, se supone que cada resistencia no depende de sus vecinas. Por tanto, las pérdidas totales son la suma de las pérdidas provocadas por cada resistencia.
Si la tubería consta de varias secciones de diferentes diámetros con varias resistencias locales, entonces la pérdida de presión total se calcula mediante la fórmula:
,
Dónde ,
, ,…, , , , …, , , , …, – coeficientes de resistencia y velocidades promedio para secciones individuales y resistencias locales.
3.6 Influencia de varios factores en el coeficiente
La mayor dificultad para calcular las pérdidas de carga es el cálculo del coeficiente de fricción hidráulica. , que está influenciado por muchos parámetros de flujo y tuberías.
El estudio de la influencia de diversos factores sobre el valor del coeficiente de fricción hidráulica se dedica a Número grande experimentales y trabajos teóricos. Estos experimentos fueron llevados a cabo de manera más exhaustiva por Nikuradze I. (1932). Se llevaron a cabo en tuberías con rugosidad artificial, que se creó pegando granos de arena de rugosidad uniforme a la superficie interior de las tuberías. La pérdida de presión en las tuberías se determinó a varios caudales y el coeficiente se calculó utilizando la fórmula de Darcy-Weisbach. , cuyos valores se trazaron en función del número de Reynolds Re.
Los resultados de los experimentos de Nikuradze se presentan en el gráfico = f(Re) (Figura 39). Considerándolo, podemos sacar las siguientes conclusiones importantes.
En la región del régimen laminar ( Re<2320) все опытные точки независимо от шероховатости стенок уложились на одну прямую (линия 1).
En consecuencia, aquí depende sólo del número de Reynolds y no depende de la rugosidad.
Durante la transición de condiciones laminares a turbulentas, el coeficiente aumenta rápidamente al aumentar Re, quedando en el tramo inicial independiente de la rugosidad.
En la región del régimen turbulento se pueden distinguir tres zonas de resistencia. La primera es la zona de tuberías lisas, en la que = f(Re), y la rugosidad Ke() no aparece; en la figura los puntos están situados a lo largo de la curva inclinada (curva 2). Cuanto mayor sea la rugosidad, antes se producirá la desviación de esta curva.
La siguiente zona se llama zona de tuberías en bruto (precuadrática), en la figura está representada por una serie de curvas 3 que tienden a ciertos límites. El coeficiente en esta zona depende, como se puede observar, tanto de la rugosidad como del número de Reynolds = F(Re, Ke/d). Y finalmente, cuando se superan ciertos valores de los números Re, las curvas 3 se convierten en rectas paralelas al eje. Re, y el coeficiente se vuelve constante para una rugosidad relativa constante = (Ke/d). Esta zona se llama autosemejante o cuadrática.
Figura 39 – Gráficos de Nikuradze
Los límites aproximados de las regiones son los siguientes:
zona de tubería lisa 4000
zona de tubería rugosa 10 d/ke
zona cuadrática Re> 500d/ke.
La transición de una zona a otra se puede interpretar de la siguiente manera: siempre que las protuberancias de rugosidad estén completamente sumergidas en la capa límite laminar (es decir,< ), они не создают различий в гидравлической шероховатости. Если же выступы шероховатостей выходят за пределы пограничного слоя (k>δ), las protuberancias rugosas entran en contacto con el núcleo turbulento y se forman torbellinos. Como es sabido, con un aumento Re el espesor de la capa disminuye y en la última zona (cuadrática) esta capa desaparece casi por completo ().
Sin embargo, las tuberías utilizadas en la práctica tienen una rugosidad no uniforme y desigual. Muchos científicos se dedicaron a dilucidar la influencia de la rugosidad natural; los más famosos fueron los experimentos de G. A. Murin (para tubos de acero).
Habiendo confirmado los patrones básicos establecidos por Nikuradze, estos experimentos permitieron sacar una serie de conclusiones importantes y significativamente nuevas. Demostraron que para tuberías con rugosidad natural en la región de transición siempre es mayor que en la cuadrática (y no menos, como ocurre con la rugosidad artificial); y al pasar de las zonas 2-3 a la cuarta, la continuidad disminuye. Los resultados de los experimentos de Murin se presentan en la Figura 40.
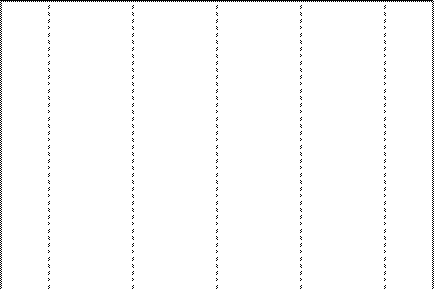
Figura 40 – Resultados de los experimentos de Murin
3.7 Fórmulas para determinar el coeficiente de Darcy
Para calcular el coeficiente de Darcy, existe una gran cantidad de fórmulas empíricas y semiempíricas, la mayoría de las cuales tienen un área de aplicación limitada. Consideraremos sólo algunas fórmulas básicas, las más utilizadas y que tienen amplios límites.
En modo laminar ( Re<2320) для определения в круглых трубах применяют формулу Пуазейля:
= 64/Re.
La fórmula se deriva teóricamente, como se muestra en la sección "Características del flujo en modo laminar".
En la región de transición del régimen laminar al turbulento λ calculado usando la fórmula de Frenkel:
λ= 2,7/Re 0,53 .
En condiciones turbulentas, hay tres zonas:
Para tuberías hidráulicamente lisas se utilizan varias fórmulas:
Más comúnmente utilizado:
Blasio λ= 0,3164/Re 0,25 área de aplicación (4000<Re<10 5);
Konakova λ= 1/(1,81 lg Re- 1.5) 2 áreas de aplicación (4000<Re<3×10 6)
Para tuberías hidráulicamente rugosas:
Altshulya λ= 0,11(KE /d+ 68/Re) 0,25 ;
Colebrook–Blanco
Los límites de uso de estas fórmulas se pueden determinar en el rango de números de Reynolds desde 10 d/K E hasta 500 d/K E.
En la región de resistencia cuadrática (el número de Reynolds es más de 500 d/K E) se aplican fórmulas:
Shifrinson B. L. λ= 0,11(KE /d) 0,25 ;
Prandtl-Nikuradze λ= 1/(1,74+ 2 litros d/K E) 2 .
Las fórmulas anteriores tienen en cuenta de forma más completa y correcta la influencia de varios factores sobre el coeficiente de fricción hidráulica. Se seleccionan entre una gran cantidad de fórmulas existentes actualmente.
La fórmula de A. D. Altshul es la más universal y puede aplicarse a cualquiera de las tres zonas del régimen turbulento. Para números de Reynolds pequeños está muy cerca de la fórmula de Blasius, y para números de Reynolds grandes se transforma en la fórmula de B. L. Shifrinson.
Preguntas de control
1. Dos modos de movimiento de líquidos y gases.
2. Experimentos de Reynolds, criterio de Reynolds.
3. Características de los regímenes laminar y turbulento.
4. Diagramas de distribución de velocidades.
5. Resistencia hidráulica, su naturaleza física y clasificación.
6. Fórmulas para el cálculo de pérdidas de energía (presión).
7. Resistencia hidráulica local, fórmula básica.
8. Dependencia del coeficiente de resistencia local del número de Reynolds y parámetros geométricos.
9. Resistencia a lo largo, la fórmula básica para calcular las pérdidas.
10. Zonas de resistencia hidráulica, experimentos de Nikuradze y Murin.
11. Las fórmulas más utilizadas para calcular el coeficiente de fricción hidráulica.